The RC Geek Blog
By: Chris Wolfe
All I wanted was to install bulkheads…but somehow ended up with 4 speed brakes instead…
We have a pretty sizable article this week which is the first in a two part series discussing how the speed brakes were built, actuated and detailed for our Frankel F4D Skyray. In addition, I’ve put together a couple how-to videos to support (the first being below). So, let’s get to it!
Fuselage ready for surgery.
In our previous article, we completed (mostly) our dorsal assembly. With that completed, we can finally move on to work on the fuselage. Typically I would go to the wings next (I generally like to work on the largest parts last), but in the case of this build, we need to have bulkheads installed in the fuselage first before working on the wings. This is so that the wing mounts and spars can be setup in the foam cores before they are sheeted.
So, this originally was going to be a quick task; cutting hatches, installing bulkheads, that’s quick right?!… With that in mind and with much vigor, I plowed on to cutting out the hatch and clearing away any fiberglass that needed to be removed; this included the area in the canopy hatch and the intakes. However, once I had that completed, I realized that getting hands into the aft fuselage (i.e. area where the speed brakes would go) once the bulkheads were in was going to make placing speed brakes difficult. So, instead, I transitioned into building speed brakes…4 identical speed brakes that will ultimately be placed near the aft end of the fuselage. It took some time given I had to build four identical ones, but the result was well worth it. So, in this post we’ll discuss the process of building the speed brakes mostly, but first we need to touch on cutting the hatches out.
Cutting Fiberglass Hatches
The first requirement for the fuselage construction was to cut the main fan hatch and clear away the closed off areas around the canopy hatch and the inlets and open them up (these are closed off for ease of layup of the fuselage). To cut the hatch, masking tape was used to line the entire perimeter which was used as a guide. From there, an Xacto razor saw was used to cut the hatch out, the tape serves as an edge to guide the razor saw while cutting. To initially cut through the glass, the front corner of the razor saw was used to rub into the glass focusing on a small area to puncture through the glass (all while using the tape as a guide) . It takes time, but once cut through, the razor saw is then used to cut the full edge of the hatch. This process was repeated for all edges of the hatch perimeter. In the case of this Skyray, the fuselage layup features carbon fiber tape lining the entire hatch area. Though, it adds stiffness to the fuselage, it is dreadful to cut with a standard razor saw as it dulls them quite quickly. So, in this case, the razor saw was used to cut through the glass and carbon, but from there a #13 Excel saw blade was employed to make most of the cuts as this saw blade was more resilient to the carbon and made it easier to cut. It had a smaller surface area, so would not catch or pull the hatch or fuselage as much
To open up the inlets and the canopy hatch area, a dremel with a 1/16″ fishtail cutter bit
was used to rough out the openings. A Dremel sanding drum
was then used to smooth the edges and fine tune the openings as desired. For the canopy hatch, this consisted of simply edging the area leaving an approximate 1/4″-1/2″ flange all around the area opening. For the inlets, this consisted of sanding the glass away all the way into the corners of the inlets to the fuselage. These areas will eventually have the internal inlet ducting fed through them when we get to that point. Note that on the inlets, I used a sharpie to highlight the corners of the inlets so as not the remove too much material.
From here, the bulkheads were test fit as they need to be in place before we can do any of the other large construction. It was at this point that I realized that if I was going to build speed brakes into the airframe, this was the time it needed to be done, before the bulkheads are installed. As large as the model is, internal access in the aft fuselage isn’t the easiest to get to, especially once bulkheads are glued in place. So, at this point, it was time to switch gears and build some speed brakes…4…of… them…identical to each other…
Speed Brakes!
The skyray has 4 speed brakes in the aft fuselage forward of the pitch trimmers; two on the top with the other two on the underside. They are hydraulically actuated having a single piston attached to the forward center of the speed brake internally. The goal is to mimic and simulate that look as much as possible with the end result being something functional and maintainable looking very much like the full size.
Cutting The Speed Brakes Out
To build the speed brakes, the first requirement was to establish the shape and location of them on the airplane. I used 2D CAD to draw them while scaling from my drawing reference (I talk more about that in this post ). I cut the shapes out of sticky backed vinyl and placed them onto the fuselage. I made templates for the location to ensure that they were all placed correctly relative to each other and the fuselage as a whole (simple paper templates were plenty sufficient).
To cut the speed brakes, the same method as described above to cut the hatch using an Xacto Razor Saw was employed here too. The vinyl speed brake acted as the template and tape edge for the saw. Again, since cutting through carbon fiber was necessary, a #13 Excel saw blade was employed to cut through it.
Building Liners and Hinging the Speed Brakes
I should note, that initially to determine the proper geometry, I first built a mockup from the first speed brake that was cut out. This allowed me to see at what height the air cylinder needed to be and the location of the horn bracket on the speed brake. Once I had that determined, I followed the steps below to build the final to be installed speed brake assemblies.
With the speed brake removed, the next step was to hinge them. To do this, an interior well/liner was built that serves to hold the hinge while also adding a scale realism to the interior. I determined the geometry of the liner in 2D CAD at the same time I drew the speed brake shape itself. I then used that as a plan and built the liner from that drawing.
The edges of the liner were made from 1/4″ balsa that was cut at about 1/2″ wide. I pre-finished one edge by smearing medium CA on one of the 1/2″ tall edges, wiping it down lightly (to ensure full coverage and remove excess) with a paper towel and then hitting it with some Zip Kicker once full covered. Using a sanding block with 180 grit sand paper applied to it, I then sanded the glue smooth and hit it with a coat of primer. The gave a nice finished sheet metal look by filling in the wood grain.
The edges were built on top of an appropriately sized piece of 1/64″ plywood that was also prefinished. In this case, the 1/64″ ply was primered and sanded a few times until the wood grain was filled and the surface was smooth. A rounded slot was cut through the middle (indicative of the full size) to allow for the air cylinder to pass through for actuating the speed brake. When built, all of the finished edges were oriented inward (the inside is what we want to have the finished look).
To hinge the speed brake, two basswood stiffeners were glued to the interior of the speed brake. A 3/32″ hole was drilled in the ends of each and a 3/32″ aluminum tube was embedded in each opening. This is so that a 1/16″ wire could be run through the tubes to act as a hinge pin. From there, the same treatment was given to the speed brake liners. In this case, I 3D printed a drilling fixture to set the holes properly for the aluminum tubing. Having a fixture helped remove any type of guessing and in the long run expedited building the 4 speed brakes. Once drilled, the aluminum tubing was glued in place following a quick test fit of the assembly to ensure smooth actuation.
With the aluminum tubing in place in the speed brake as well as the liner, the speed brake is hinged by placing it atop the liner and inserting a 1/16″ diameter wire (90 deg bend on one end) all the way through all of the tubing (liner and speed brake). Note that it was necessary to clearance some of the top of the balsa edges (speed brake to liner fit) so that the speed brake would set properly based on the speed brake contour. At this point, we have a fully hinged speed brake and we can proceed to the next step…actuation.
Actuation
To actuate the speed brakes, I decided to go with air cylinders vs servos. The reason for this is two fold, 1) it is about as scale as possible and provides the perfect look within the speed brake compared to the full size airplane and 2) air cylinders can be setup with very positive closing force to minimize the chances of blow-back and the speed brakes potentially opening in certain phases of flight (high g’s, high speed, etc.). Setting up servos in this manner will ultimately burn them out unless an over-center lock is setup which would have been difficult.
The air cylinders are Air Power 1″ stroke (obtained from DreamworksRC ) and are about as light weight as you can get in an air cylinder of the size. The cylinder is attached to two lite plywood brackets that are glued to the underside of the speed brake liner. The height was determined through the mockup by ultimately finding a height that worked best that closed the cylinder well and also pushed it open to an angle that appeared correct. To hold the cylinder in place at the bracket end, a single screw through the hole at the end of the cylinder is used that screws through the brackets. On the speed brake end, I made a 3D printed horn bracket and glued it in place. A du-bro ball link was used at the end of the air cylinder which slips into place into the horn bracket while two 4-40 bolts hold it in place.
Note that in order to get really positive pulling force on the speed brake when closed, the wood brackets were glued in place such that when the speed brake is fully closed, there is about 1/32″-1/16″ of travel left in the air cylinder. This results in an extremely strong closing force once the air cylinders have air in them.
Here’s a video to help illustrate a bit more what has been discussed to this point.
At this point, we now have 4 built speed brakes. However, before we move on to installing them into our fuselage, it’s best that we do ALL detailing of the internals first. Ideally, the internals would even be painted before we install them. So, next time we will get into detailing the interior wells of the speed brake including application of raised rivets; Good times!
The post How to Build an RC Jet – Part 7 appeared first on The RC Geek.
The RC Geek Blog is your place to learn about all aspects of the RC hobby. Learn to build, design, drive or fly that RC project you’ve always wanted to build, but have been intimidated to try. This blog is here to help you on your journey and provide tips and tricks as you go! My hope is to inspire builders both experienced and new! So, welcome, please look around, it’s an exciting beginning! I’m currently documenting my latest competition scale RC jet build, a Mark Frankel F4D Skyray, along with some other fun tips and videos. If you can’t find what you’re looking for on this front page, click on any of the categories to the right and it will show just posts related to those categories. Please feel free to add comments and/or contact me directly if you have questions, I’m here to help! And don’t forget to check out my YouTube Channel, I post new videos every week!
Subscribe To Our Blog Now
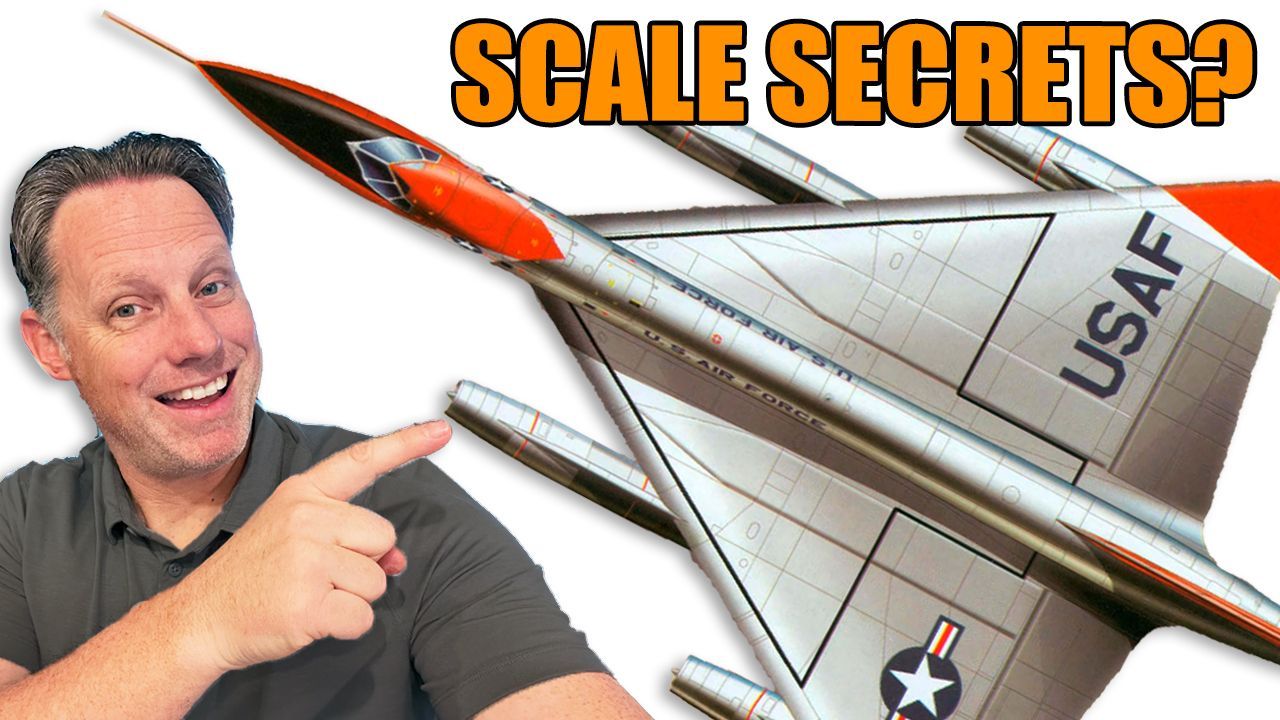
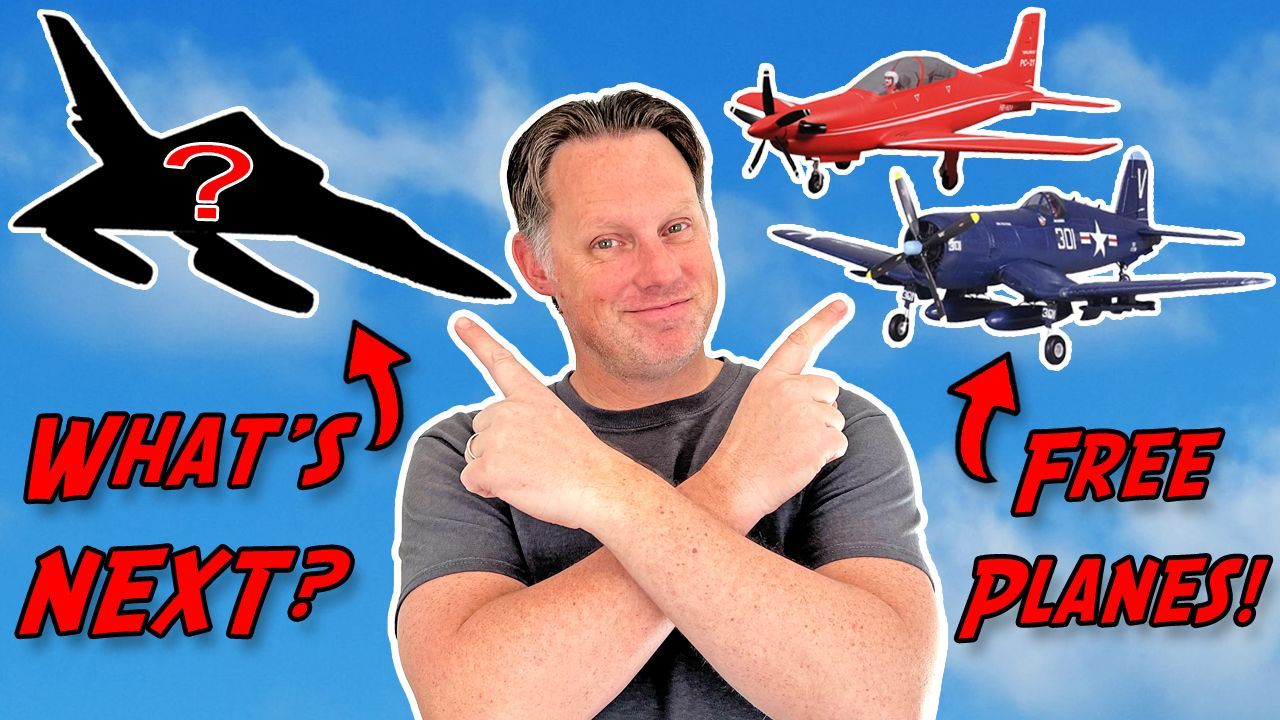
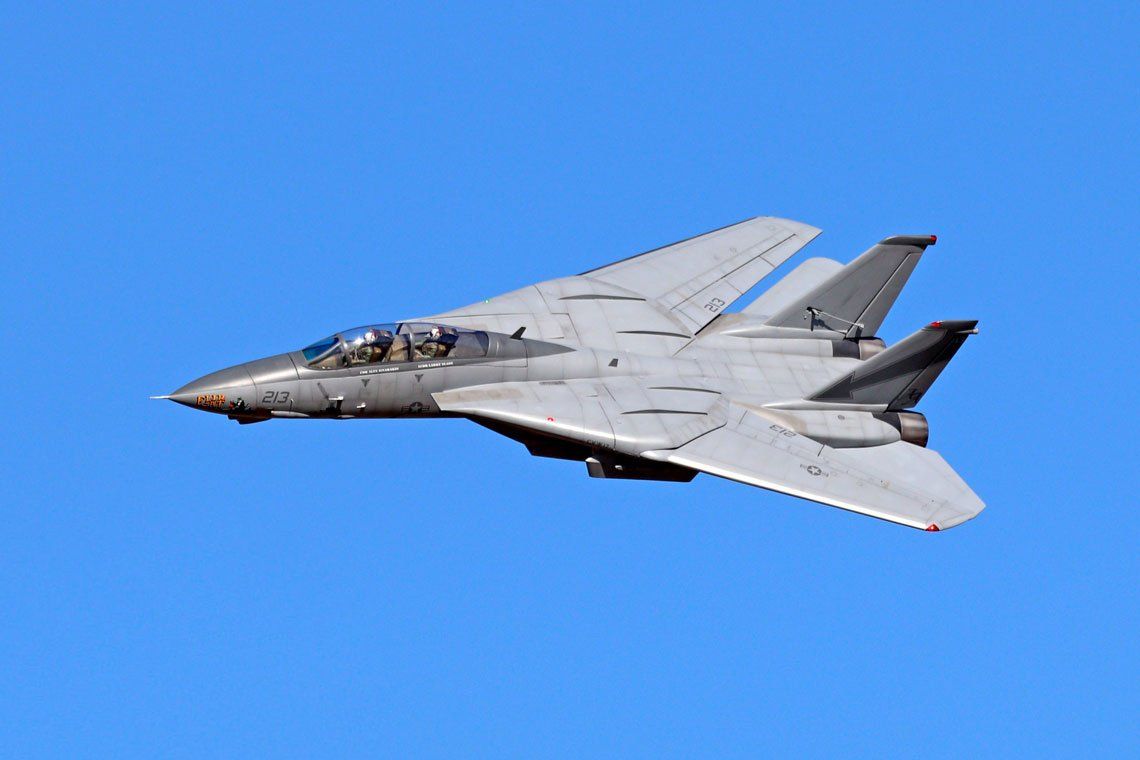
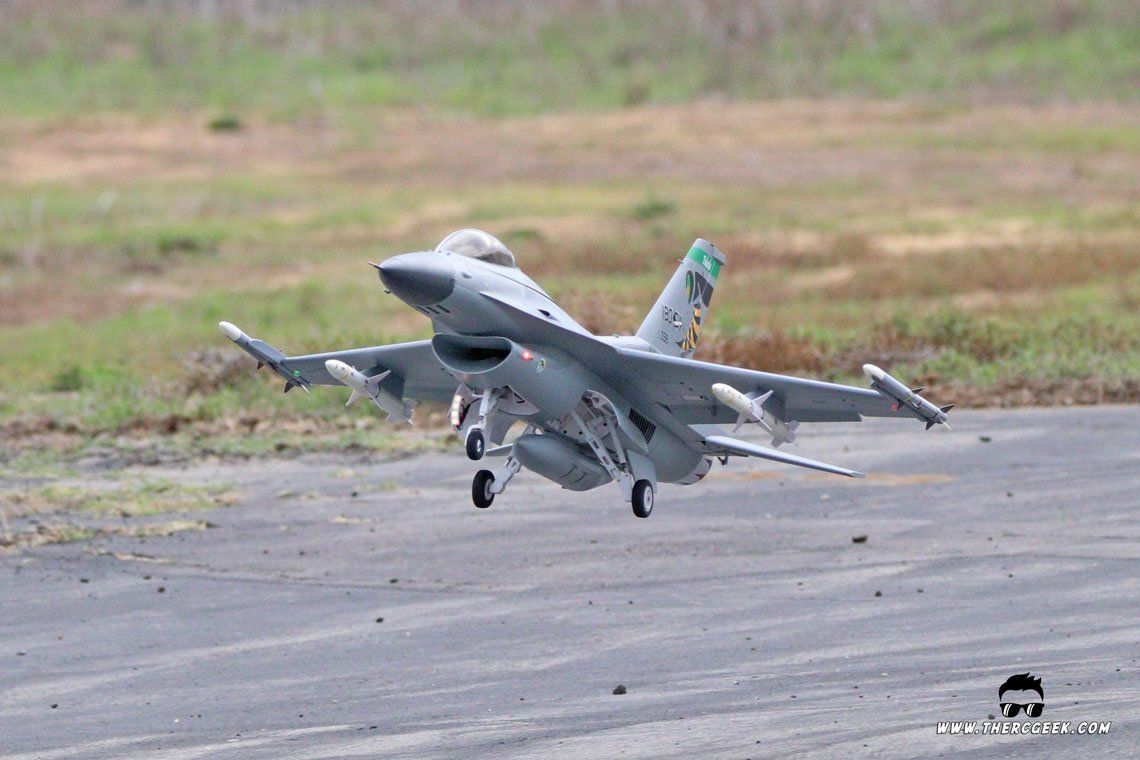
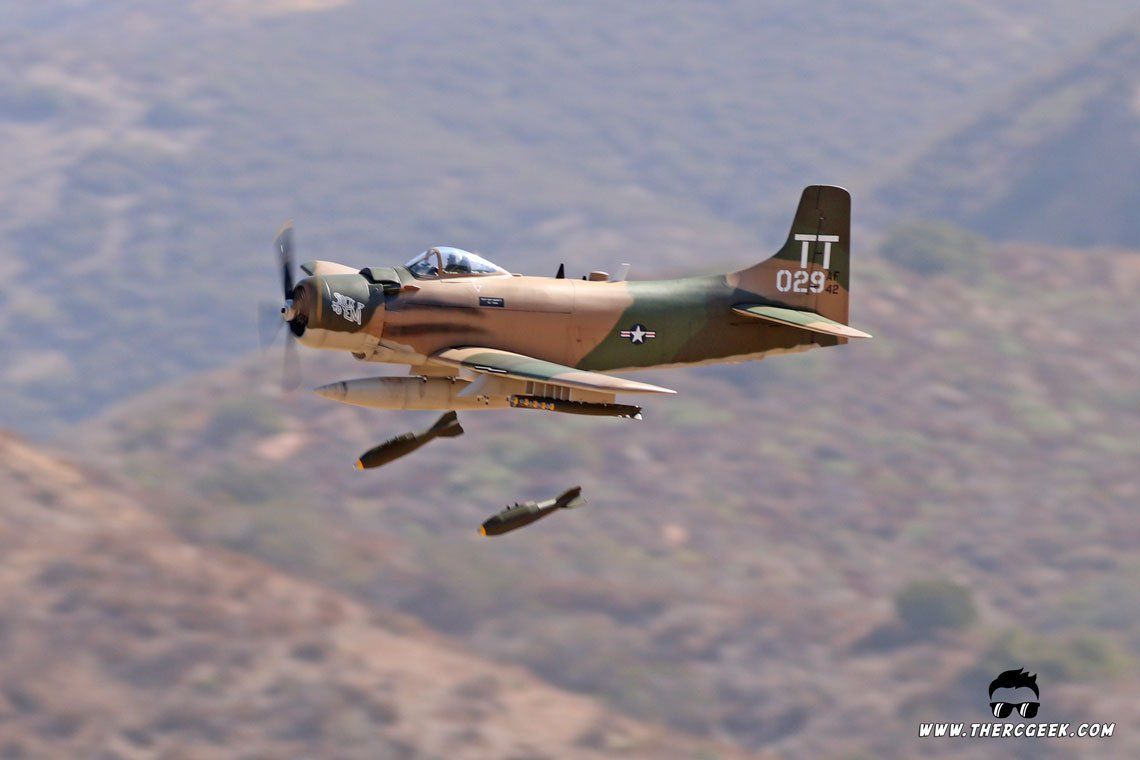
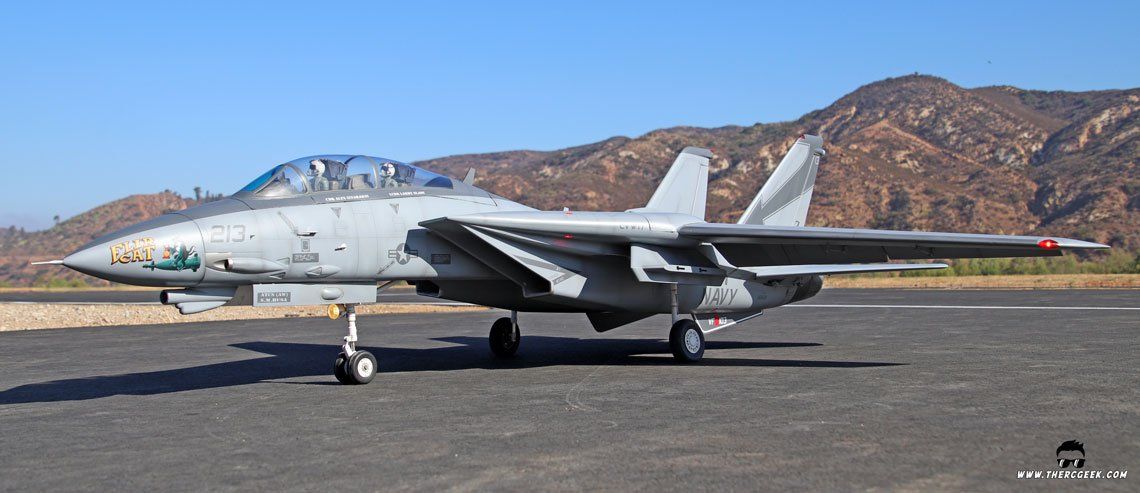