The RC Geek Blog
By: Chris Wolfe
Decals, Vinyl and Paint Masks…oh my!
The topic of aircraft markings and making decals was touched on a little bit in my How to Refinish a Foam Warbird series and the request to expand on it a bit has come up a few time since then. So, here’s a bit more extensive walk through of my process of making and painting markings for my airplanes.
Color and Markings are one thing that I’m very particular about on my scale models. I’m so particular in fact that I will usually make my own decals and paint masks as opposed to outsourcing. Ultimately I do this because I actually enjoy the challenge of it (when it’s going well of course) and this gives me full control of the sizes of all of the markings since it usually takes multiple iterations before having everything just the right size. Also, my preference is to paint whatever markings I can and in the case that the markings may be too small to paint, I will move to waterslide decals. In some cases, I will even use a combination of paint (or vinyl in the case of my “Lady Alice” ) and decals to create a single marking. Obviously, there are always limitations when doing your own markings and so in the case I just don’t have the capability to make what I need, then it’s time to outsource.
Since I’m a scale fanatic, my goal in making markings is always to recreate markings as exhibited on a full sized aircraft. This article is written pursuant to that, however, the techniques are extensible to any type of markings on virtually any type of model and/or surface.
First Things First — Documentation and Resources
Now, if we’re to the point of markings, then we’ve already chosen a paint scheme. Ideally, said paint scheme is accompanied by a nice set of coloring-diagrams with multi-views showing all of the paint diagrams and markings (especially if for competition). At the very least, we have a picture and an idea of what the rest of the airplane looks like. I will typically look to plastic model decals here truthfully. If I don’t have those, then I will try to find something that I can find a number of pictures of through google searches and other sources — this includes google searching squadron badges, and any other individual markings if that’s on the airplane and I can’t find a decent picture of it. I find a lot of inspiration through plastic model websites and they often have a great selection of paint schemes with sources to the decals used. The nice thing with plastic model decals is that they are a great source for scanning and drawing markings from too. A few of my go-to sites are:
www.aircraftresourcecenter.com – A great community of plastic model resources from decals reviews, to kits, etc. If you’re looking for paint schemes, look at the built model gallery and decal reviews. It also has a dedicated section to “Aircraft Walkarounds”
www.cybermodeler.com – A great community of plastic model resources from decals reviews, to kits, etc. If you’re looking for paint schemes, look at the built model gallery and decal reviews.
www.modelingmadness.com – A great community of plastic model resources from decals reviews, to kits, etc.
Creating the Artwork
In order to make any type of markings it requires artwork. This can be sourced from a number of places, but ultimately the medium of the marking (decal or paint) will determine what type of file is required. For making waterslide decals, simple image files are fine, even those that have been downloaded directly from the web. However, in order to ensure a crisp and clean print of the decal, unless you’re able to find a high resolution image of what you’re looking for, it really does require drawing your own in a program like Corel Draw. This also allows the use of vinyl cutting (if you have a cutter) from the Corel Draw
files since it is a vector line type of program which can export files in a CAD file format. Otherwise, if painting markings, you’ll need a template to cut from whether you’re cutting by hand (a hardcopy drawing) or with a vinyl cutter (CAD file).
In creating artwork, this is where plastic model decals really come in handy. I will often use them as a basis for making larger markings. Scanning and drawing over them works the best. Otherwise if you scan them and try to print them at a larger size, they will just be fuzzy and won’t look right. I’ve often found errors even and corrected them in this process. Also, tracing over markings found in pictures works too. The whole reason we have to do this is simply because we don’t have what we need at the right resolution.
Water Slide Decals
Printing your own water slide decals is an easy way to create markings for a project and is simply done by printing your desired artwork onto decal paper. It’s important to note that when doing this, we can realistically only apply dark colored decals over lighter colors (Black will go over any color of course). The issue is that both inkjet and laserjet printed decals are semi translucent, so when applied to a white background has the perfect color, but when applied over a dark background takes on the color of what is underneath. Now there is decal paper that has a white carrier film that is available to use that’s supposed to provide better decal color when going over a dark color. However, it still has the same issue taking on the colors underneath it. Also, it requires that the decal be cut perfectly around the artwork so you don’t see any unwanted white carrier film which is just a pain to deal with. This is why when I need to place a decal over a dark color, I will resort to paint masks and/or cutting vinyl backings (discussed further down). Note that when placing decals, the use of “ micro set ” and “ micro sol ” are highly recommended as they help the decals adhere to the surface better. The “ micro sol ” actually softens the decal so that it pulls into any recesses or details, so only apply it once the decal is set and then left to dry.
When we talk about printing decals, it is important to discuss the type of decal paper to use as there are two kinds that are readily available — inkjet printer decal paper and laserjet printer decal paper. My preferred paper is for the laserjet. The reason is that it does not require a clear coat as a carrier. As a result you get a much thinner and more robust decal. The only drawback is that it requires printing on a laser printer. If you don’t have immediate access to one, find a print shop and have them print it for you for a few bucks, it’s worth it! Here’s a quick explanation of the two types of papers.
LaserJet Decal Paper – This paper is intended for use with laserjet printers which are typically what you’d find in offices and print shops. These decals are immediately ready for application straight out of the printer (no clear coat necessary). Also, the decals once applied are robust enough to handle all types of clear coats we use on our models.
InkJet Decal Paper – This paper is intended for use with inkjet printers which are the most typical types available at home. It requires multiple coats of a clear coat over it (like this Krylon ) to seal the printed artwork and also provide a carrier film. Be careful not to apply too heavy a coat at one time as the artwork will run. Also, once applied to the model, a heavy solvent based clear coat over the artwork could also cause runs too since we can’t use a solvent based clear coat to initially seal the decals. Using Laser Decal Paper you won’t have any of these issues.
Paint Masks
Whenever possible for my scale competition airplanes, I will paint my markings. This goes so far as painting lettering, stars and bars, the whole gamut. Obviously, it’s not always practical to paint some markings, especially when we’re talking about really small details and lettering or multi-colored badges and that’s usually where the decals come in.
To cut paint masks, I use a vinyl cutter. I use a Roland SV-12 and absolutely love it! To cut a mask simply requires a CAD/vector line drawing of the object to cut. It’s sent to the cutter the same as you would printing something on a piece of paper only the machine cuts vinyl. It does have pre-packaged software which can be used to draw the markings, but in most cases I simply use Corel Draw and/or a CAD program (Rhino 3D works well for this). I generally use a lower tack vinyl with a little more thickness to it since I don’t want the vinyl permanent on the surface.
Obviously, a vinyl cutter is a nice to have and for those who don’t have one as an option, with a little extra work paint masks can be cut by hand (my dad still cuts his paint masks by hand). The same vinyl can be used as is used with a cutter though. Again, it requires having the desired artwork, but in this case a printed hard copy should be lightly spray-glued ( 3M 77 does the trick) to the paint mask material. From there, the mask is cut by hand using a sharp Xacto knife. For straight cuts, use a metal straight edge, for circular cuts, a circle template works as well as a protractor with a blade in it and for those hard to cut areas, cutting by hand is the way to go.
With the masks cut, it’s a matter of placing them onto the aircraft and painting them appropriately. In some cases where multiple colors are necessary (like stars and bars) multiple masks will need to be cut. For example, in the case of a star and bar, the whole outline would need to be cut to spray the white. Then masks are placed to protect the white (center bars and star) and then the blue would be sprayed. Lastly, the red bars would be added.
The Combo Platter
As mentioned with the decals, they really only work over a light background. To get around this, I use a combination of paint masks and/or cut vinyl and decals. Also, for artwork needing to be a specific color to match other painted areas on an airplane, I use this method as well. Where this works best is for badges or insignias that have multiple colors; I’ve also used this method for multi-colored lettering also (e.g. “Lady Alice” text on my P-51
). What I will do in this case is cut a paint mask that encompasses the complete outline of the marking, place the mask on the aircraft, and then paint that area white (or the necessary color). From there once the paint is dry and the paint mask removed, the badge/insignia decal can then be placed over the painted area and completes the marking. Also, in cases I need specific colors to match paint, I paint the area the necessary color and then place a decal of the detail markings. An example of this is the “BlueHawk” on the tail of my JHH
A-7. The paint mask was placed and the area painted white. I then masked any areas needing to stay white (beak and claw areas) and painted the area blue. Everything else (black details and yellow) were placed as a single decal.
When What I’m Able to Make Won’t Work
With all of these methods, sometimes, there just comes a time where we can’t make what we need to. Mostly this comes with fine light colored detail lettering that needs to be placed over a dark color. In these cases, we have to outsource. The primary company I have used is GetStencils.com. They do full vinyl cut paint masks as well as dry transfer markings.
If you’re looking for some pre-made vinyl graphics, callie-graphics
is a good option and very affordable. Callie can also cut paint masks on request too. I’ve had a few friends use this service and they’ve been happy with the result. The vinyl graphics are printed vinyl so don’t always provide a painted look up close, but from a short distance the result looks very nice.
Now, I recently became aware of a process that uses a screen printing process for making paint stencils. I will be exploring this in the future, so will definitely report the results. The opportunities from this process may finally fill the gap in creating small detail lettering at home.
WE’LL COVER THIS AGAIN…
I’m sure I forgot something, but we will visit this in more detail at a later date. I intend to make all my own markings for my Frankel F4D Skyray project and so plan to discuss the details of what I do specifically on that airplane. Until then, hopefully this provides some good details for you and you can always email me if you have questions. See you at the field!
The post From the Bench — Tips for Making Your Own Aircraft Markings appeared first on The RC Geek.
The RC Geek Blog is your place to learn about all aspects of the RC hobby. Learn to build, design, drive or fly that RC project you’ve always wanted to build, but have been intimidated to try. This blog is here to help you on your journey and provide tips and tricks as you go! My hope is to inspire builders both experienced and new! So, welcome, please look around, it’s an exciting beginning! I’m currently documenting my latest competition scale RC jet build, a Mark Frankel F4D Skyray, along with some other fun tips and videos. If you can’t find what you’re looking for on this front page, click on any of the categories to the right and it will show just posts related to those categories. Please feel free to add comments and/or contact me directly if you have questions, I’m here to help! And don’t forget to check out my YouTube Channel, I post new videos every week!
Subscribe To Our Blog Now
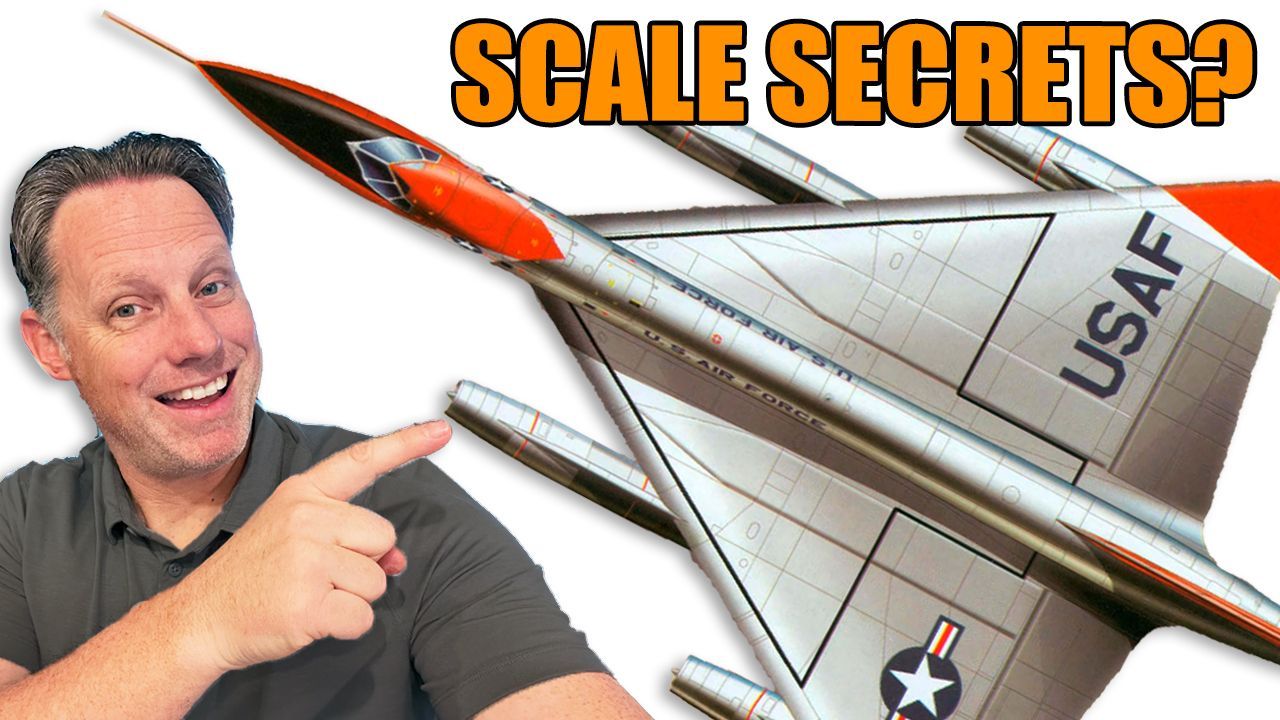
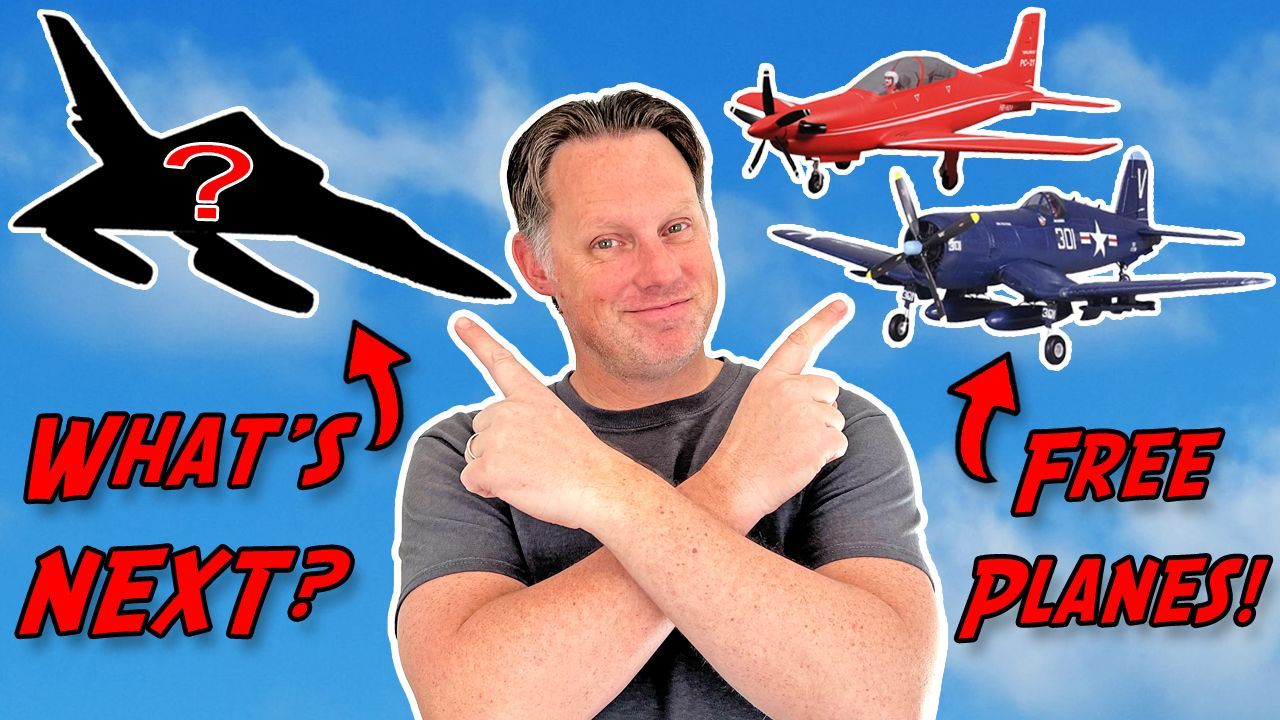
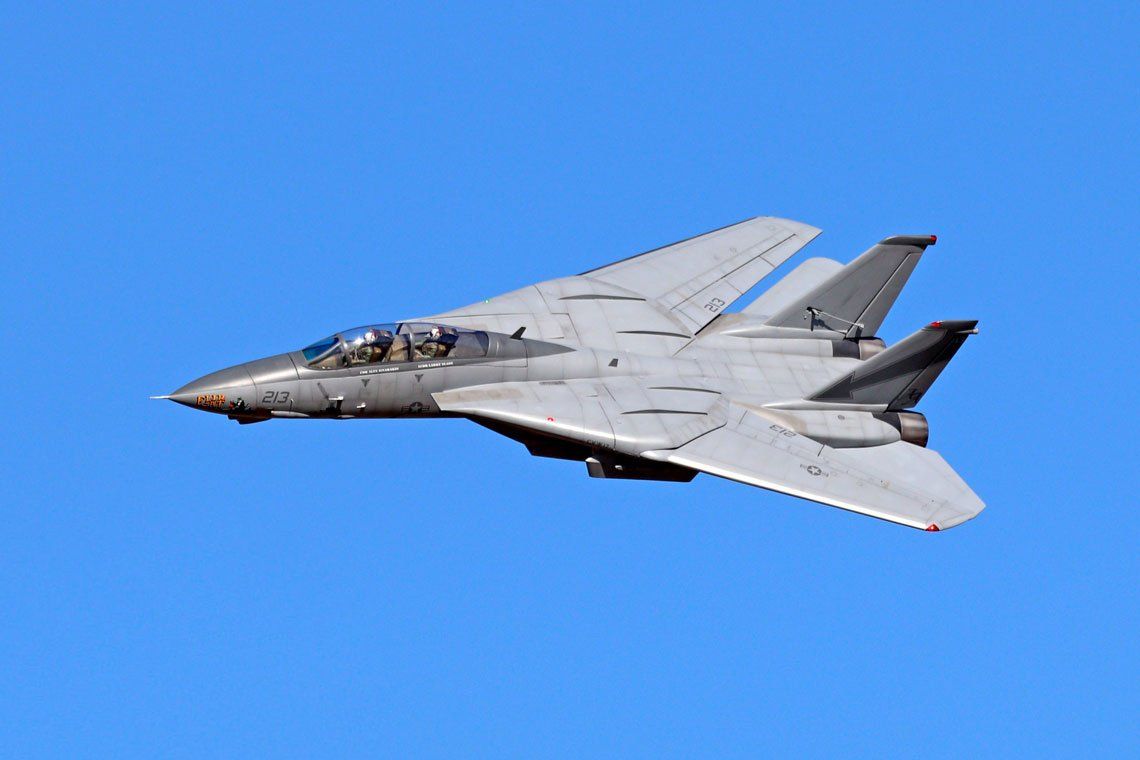
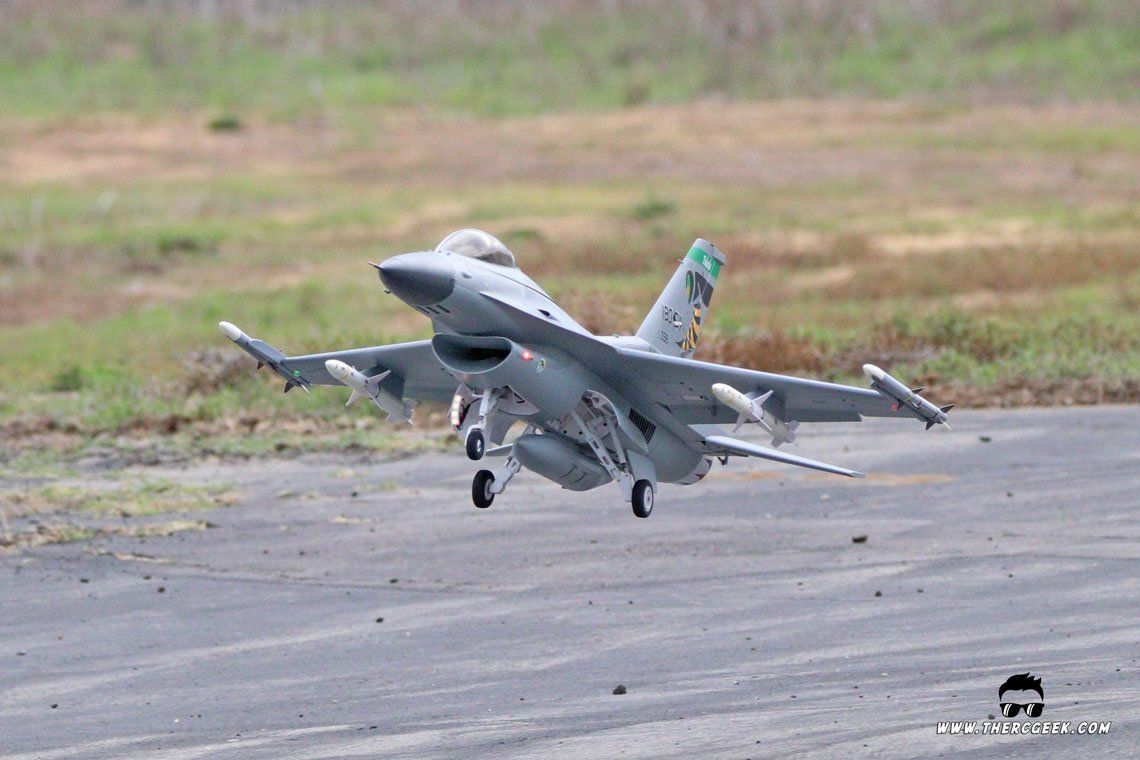
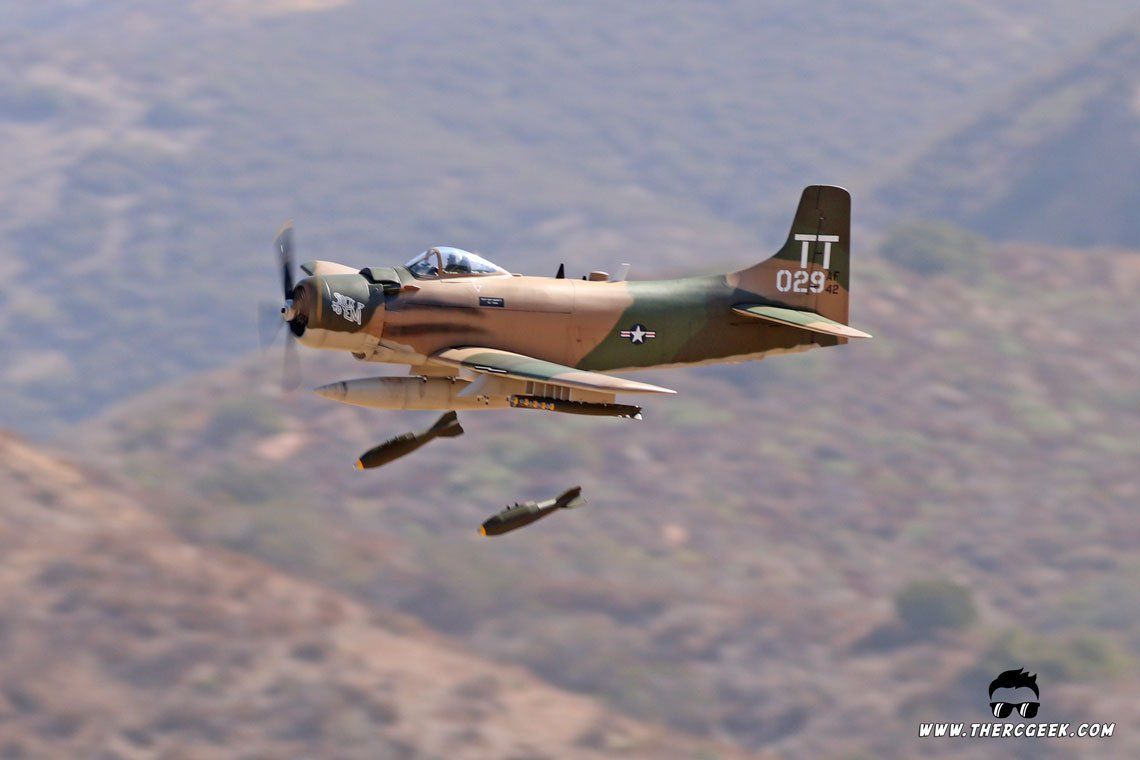
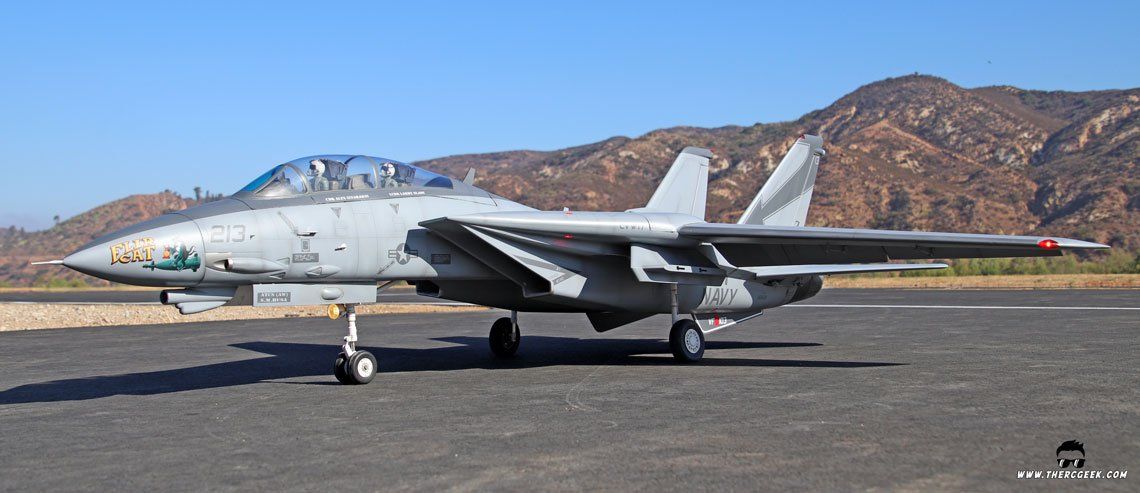