The RC Geek Blog
By: Chris Wolfe
With the 2016 Scale Master’s Championships
just a few weeks away now, here’s a little glimpse into the journey in getting there. In addition to this, I also had some pains at the Gilman Springs qualifier too which I wrote about in my coverage from the event. So, it’s been an interesting year that ultimately has improved the airplane as a whole, but not without a lot of frustration and multiple stints of repair work through the year. But, with a little persistence (and lots of complaining), I think we’ve got it all worked out and the Mirage IIIRS is ready to go big at Woodland-Davis!
It has been said there are two types of model airplanes… those that have crashed and those that WILL crash…
Well, if you follow this site on Instagram or Facebook then you know that the inevitable happened! My competition Mirage IIIRS crashed! I was at an event back in October last year and for whatever reason, the fan wasn’t making the power it typically does during takeoff. The takeoff roll was sluggish and instead of aborting and taking home a perfectly fine airplane, I forced the airplane off the ground thinking it would be ok once airborne. Unfortunately, that wasn’t the case and I couldn’t get enough altitude to get the speed up and the airplane ended up landing in a few large bushes. I walked up to the airplane expecting the worst and found it upside down but thankfully mostly in tact. I was very fortunate! The most damaged area was the nose section being broken but thankfully still connected to the airplane. I later discovered that the lack of thrust was likely due to a combination of tired batteries not holding voltage under load and a partial blockage in the exhaust duct being caused by some loose tape that I was unaware of. Thankfully it was repairable and so I thought it would be a good opportunity to discuss some basic fiberglass repair. Oh, and the lesson here??
LESSON OF THE DAY: If your airplane isn’t doing what you expect it to, abort and troubleshoot!
NOSE REPAIR
The most impacted area from the crash was the nose. Though technically still attached to the fuselage, it was pretty “crunchy” and loose. Both sides of the nose were cracked just forward of the inlets below the canopy. The right side took most of the damage which is the side I’m guessing impacted the ground first (the canard was also cracked on this side too). Also, the whole front camera screen and pitot tube were gone from the very front and nowhere to be found.
The first thing to do was to re-set the nose to get it back in place. This was done simply by piecing the bits back together on either side and using thin and medium CA to glue it all back. This was simply to hold it in place so that a more structural glass repair could be done. With it all tacked back together, some 2 oz cloth was cut and placed on the inside of the broken area through the canopy hatch area. Note that I clamped a couple hardwood rails to the nose to ensure that the nose remained straight during this process. From there, I used a laminating epoxy to wet out the cloth while it was in place in the fuselage. Since I had it available, I used the resin system that my folks use for their fuselage layups (not a readily available resin). A good and easily accessible option is West Systems 105 with 205 or 206 hardener. I know a number of folks who use this resin with excellent results. The nice thing with the West Systems is that there are different hardeners available that allow for a faster or slower cure time depending on what you need. Now, to apply the resin, I used a cheap disposable paint brush (at 50 cents, we spared no expense!) to wet out the glass cloth while the cloth sat in place over the area needing repair inside the fuselage. In applying the resin, less is more as you don’t want to apply too much. It should be applied as necessary simply to wet out the cloth…remember, more resin = more weight! The cloth should change color but not be overly glossy (glossy areas are typically resin pooling). To soak up any excess resin, I simply applied some toilet paper to the wet cloth, tapped it with the resin brush and peeled it away. From there, we let it cure and come back to start the exterior clean up work!
To do the cosmetic repairs, I used USC Icing which is a lightweight finishing putty to fill all of the affected areas from the crash. A sanding block was used to sand the contours and smooth it all out once the filler was cured. I usually have an assortment of different sized sanding blocks with different grit sand papers to do this work. There’s no one size fits all, but usually I resort to about a 6″ to a 12″ sanding block. A few passes were required to get the contours smoothed out and cleaned up. Once I was happy with that, then I locally primered all of the effected areas with Evercoat Automotive Primer.
To fix the tip of the nose where the beveled camera window and pitot tube are at the front, I had to get a little creative. I had to build back up the material as there were pieces missing that we weren’t able to locate in the crash. To do this, I glued some 1/16″ balsa wood on the inside of the nose where the nose pieces were missing. From there, I added Icing filler
over those areas (the wood served as a shelf for the filler). The filler was contoured with a sanding block to match the nose shape. The last item of business was to replace the brass tube pitot receiver on the top of the nose. This was done the same as was done originally. The area where the pitot receiver tube was to go was opened up using a dremel. From there a brass tube was epoxied into place which acts as the pitot tube receiver (an aluminum pitot tube slides into the brass tube when on the airplane). Lastly, Icing
was applied and sanded to finish out the contours around the pitot receiver and the rest of the nose. Since the nose front is a camera window, I closed it all up with a clear plastic face and masked off the camera window contour in prep for primer and paint touchup.
WING REPAIR
The wing repairs were pretty simple. The leading edges were all chewed up along with a couple of the pylons. To repair the wing leading edges, I first hardened up the exposed balsa wood with some thin CA (necessary so the Icing filler will stick to it). From there, I simply filled all of the affected areas with Icing Filler and sanded it all to match the wing leading edge contours again. From there a couple light coats of primer were applied focalized in those areas and it was ready to touchup the paint.
PAINT TOUCHUP
Matching the paint can be difficult in these repairs. Since I built and painted the airplane, I have plenty of paint to spare! If you’re repairing an ARF or something someone else built, then it’s probably best to have paint matched and mixed. Even having the paint on hand, the colors do tend to change tones slightly from sun exposure and whatnot (using a non-yellowing clear coat is critical to avoid a good portion of this!). So, to blend it all, I decided to repaint the entire nose. Also, localized areas around the inlets and the wing leading edges I sprayed using a wider spray pattern to effectively create more of a ‘blend’ on the paints. Thankfully, the shades all matched up very well and any tonal differences really just look like touched up panels and areas that you would get on the full sized airplane. The most difficult to blend was the underside light color based on the weathering that had been done. So, using some creative washes, I blended the underside colors as much as possible. Though not perfect, it’s certainly good enough as the full size is never perfect either! Note that sometimes it’s better to touch up the paint by masking off areas. Since I was dealing with larger areas and solid colors, I opted to go with the wider spray to help it all blend.
Once all of the paint was touched up, it was a matter of re-applying the panel lines and raised panels onto the airplane that were missing as a result of the repairs. For panel lines, I re-applied them the same as initially made. I plotted them out with a pencil and then use a double ended scribe
with rulers and circle templates, I scribed the panel lines into the paint. Raised panels were done using cut vinyl. For raised panels, I like to paint them separately from the model as this gives a slight color variation which accentuates the paneled look which adds to the realism. Once all of that was done, the weathering was re-applied to help dirty up the freshly painted areas. To do this, I like to brush Raw Umber acrylic artists pigment
onto the surface over the details and then wipe it off with a paper towel soaked with some Tamiya Acrylic thinner. As it is wiped off, the pigment remains in the panel-line recesses and around the raised panels. How dirty the finish is simply a function of how heavily the pigment is wiped off. My MO here is less is more usually. I do plan to cover this specifically in a separate article in the future.
With everything all touched up again (including reapplication of some dry transfers) and finalized I finished it all off by re-applying a clear coat over the entire airplane. Instead of localizing the clear to just the repaired areas, I applied it to the whole aircraft to help blend it all back together which it did. It gave the airplane again a nice uniform finish like it had before the crash. Note that I don’t apply a heavy clear coat, it’s mostly just a dusting since it’s really only applied to even out the paint finish and protect the weathering work that’s been done. For clear, I use a non-yellowing lacquer satin.
FAN TROUBLESHOOTING
Troubleshooting the fan was a must. There’s no reason to fix the airplane if we don’t understand what happened! The E-Turbax fan and Neu motor had been bullet proof for many years and so understanding what went wrong was paramount. Upon pulling the fan from the airplane, the first thing I noticed was that there was some tape hanging inside the duct. You see, for ESC cooling, I like to tape the ESCs to the top of the exhaust ducts exposed in the airflow as this helps keep them extremely cool during operation. I typically tape on the outside, but at one point I had placed a piece of tape on the inside of the duct across the ESC. Well, unknown to me, it was now hanging well into the exhaust flow. At first glance, I wasn’t too concerned. I ran the system on the bench which showed decent numbers. However, while running the fan in an instant the tape started fluttering inside the duct and I saw over a 1 lb decrease in thrust and the tone of the fan changed radically. In remembering what occurred when it crashed, the fan didn’t sound right on the roll out which must have been the tape fluttering. Very interesting! Also, the batteries were old and seemed to be struggling. So the verdict was that the combination of the tape fluttering in the duct with the tired batteries not putting out the power they should have caused enough of a performance decrease to make the airplane power marginal. Ultimately, there was nothing wrong with the fan or motor which is good!
Since I had the fan out of the airplane, I thought it would be worth installing and trying a JetFan 120 in the airframe. The motor used was a Neu 1917/1Y (590Kv) which based on the specs would give about 16 lb thrust at about 90 amps using 12 lipo cells. In bench testing these numbers proved to be about right. With the same tired batteries from the crash, I was seeing about 15.5 lb thrust at about 85 amps. This was good enough for me, so the fan was installed into the airplane and has since proven to be an awesome power system for the mirage. With the lower current draw, the flight times have significantly increased which is ideal for competition and the overall performance is actually slightly better…what really seals the deal is the sound! It’s the most turbine sounding EDF installation I’ve heard! Note that the diameter of the fan is slightly less than the E-Turbax which the inlets were designed for, so I CAD modeled an adapter ( available through my 3D Printed Products Page ) that I then 3D printed on my Robo3D. Also, the recommended exhaust for the fan is 4″. Based on the afterburner lights I have in the airframe, I was limited to 3.75″ exhaust diameter which has proven to be fine thus far. In ground testing, I didn’t see any difference in current draw running the fan without the exhaust or with the 3.75″ exhaust which told me that the it wasn’t struggling to much.
Here’s a quick flight video to give an idea of the JetFan 120 (note the sound!)
For comparison, here’s a vid with the original power system.
Next time we’ll talk about building detail parts such as pitot tubes and antennas as I lost a few in the crash and thus had to re-build them. Until next time, I’ll see you at the field!
The post How to Repair Fiberglass & Fiberglassed Parts and Touchup the Paint appeared first on The RC Geek.
The RC Geek Blog is your place to learn about all aspects of the RC hobby. Learn to build, design, drive or fly that RC project you’ve always wanted to build, but have been intimidated to try. This blog is here to help you on your journey and provide tips and tricks as you go! My hope is to inspire builders both experienced and new! So, welcome, please look around, it’s an exciting beginning! I’m currently documenting my latest competition scale RC jet build, a Mark Frankel F4D Skyray, along with some other fun tips and videos. If you can’t find what you’re looking for on this front page, click on any of the categories to the right and it will show just posts related to those categories. Please feel free to add comments and/or contact me directly if you have questions, I’m here to help! And don’t forget to check out my YouTube Channel, I post new videos every week!
Subscribe To Our Blog Now
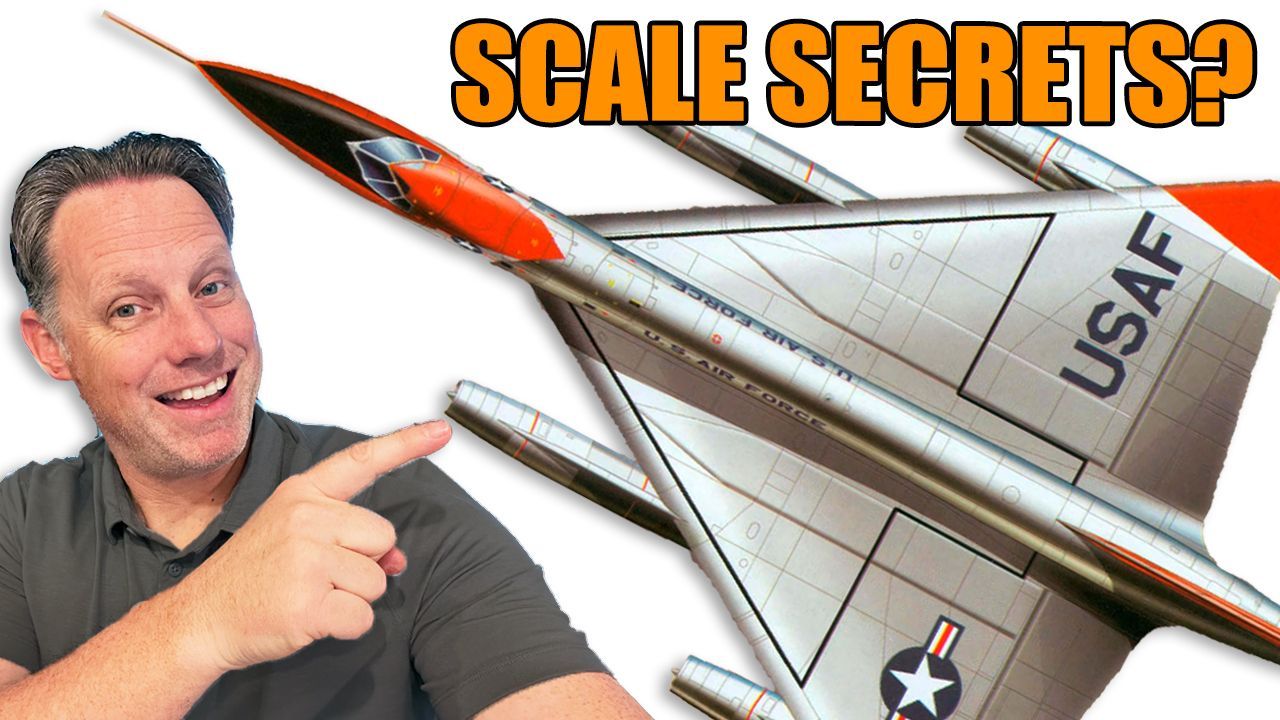
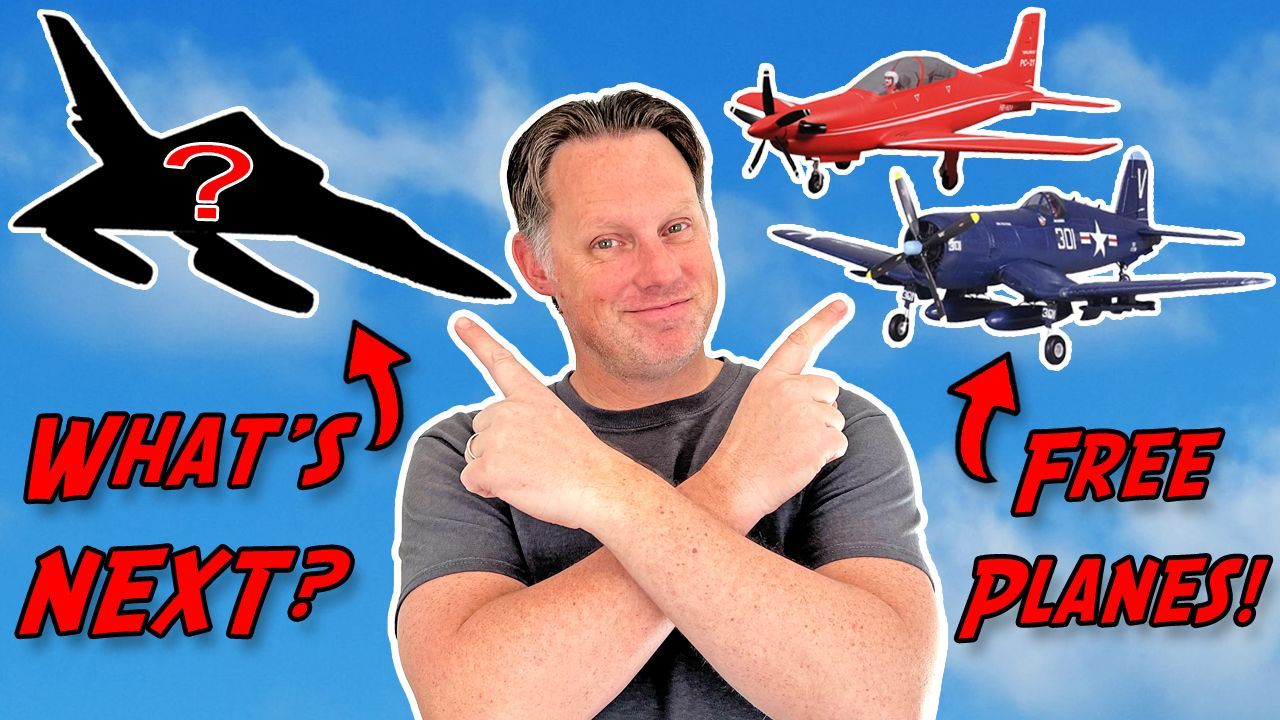
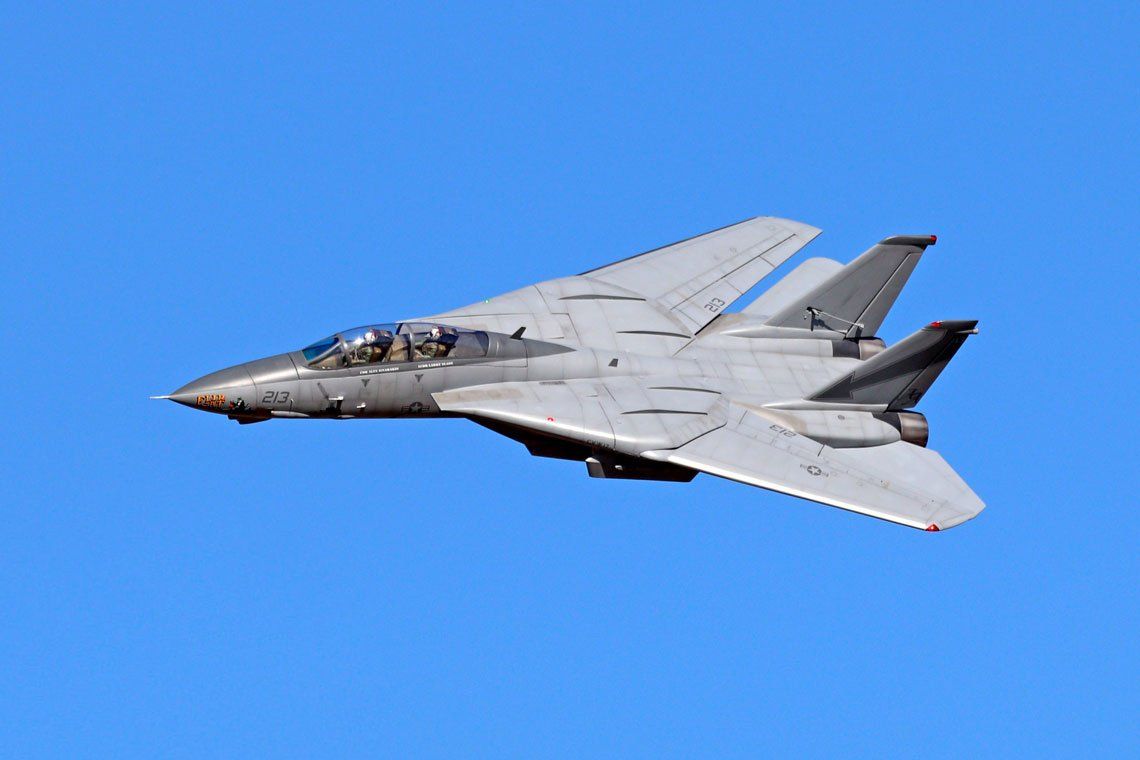
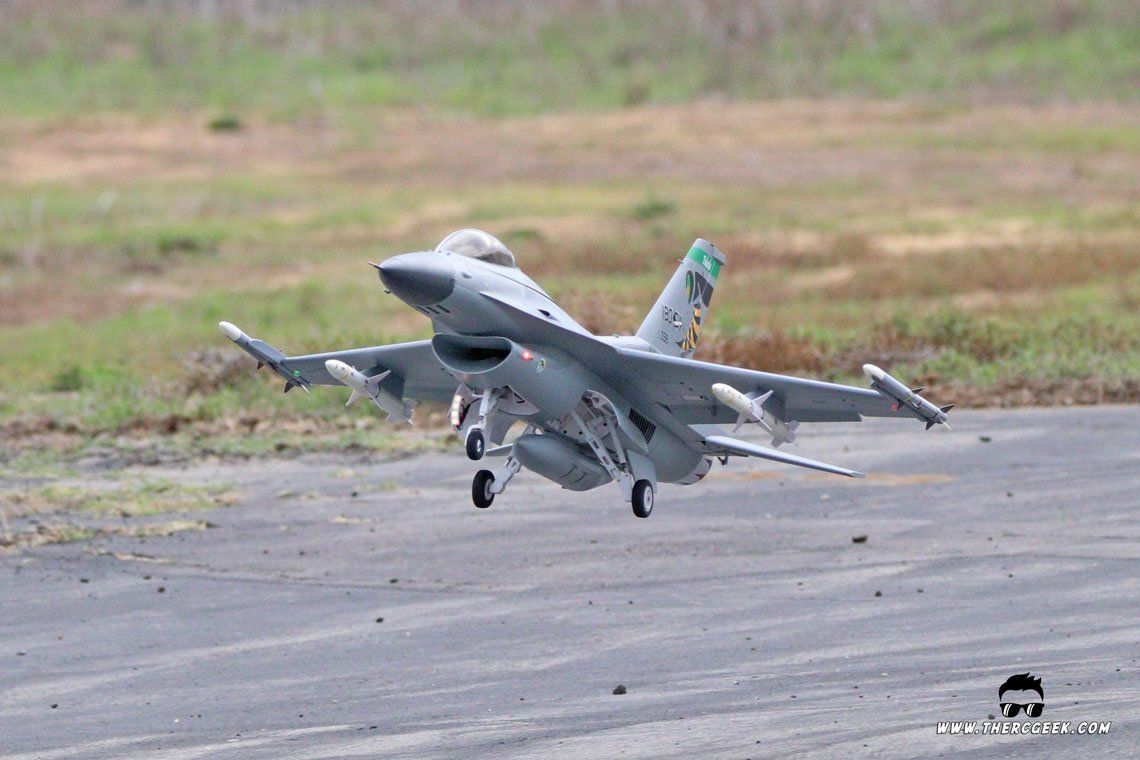
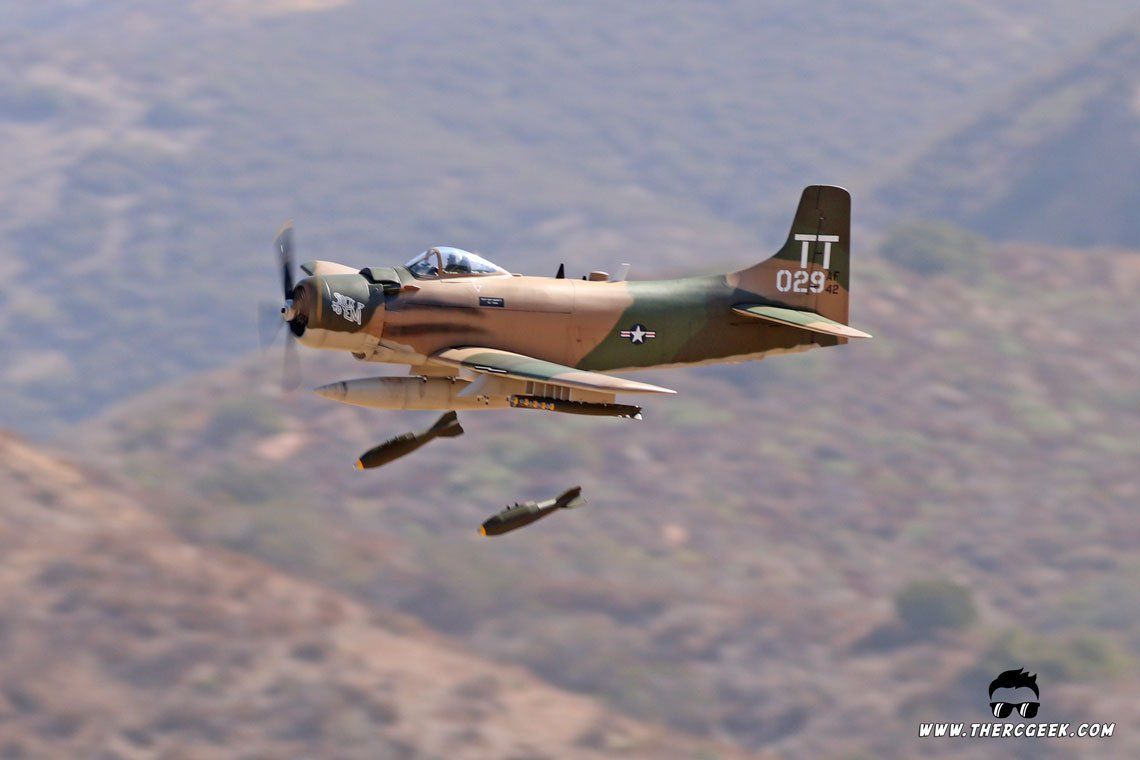
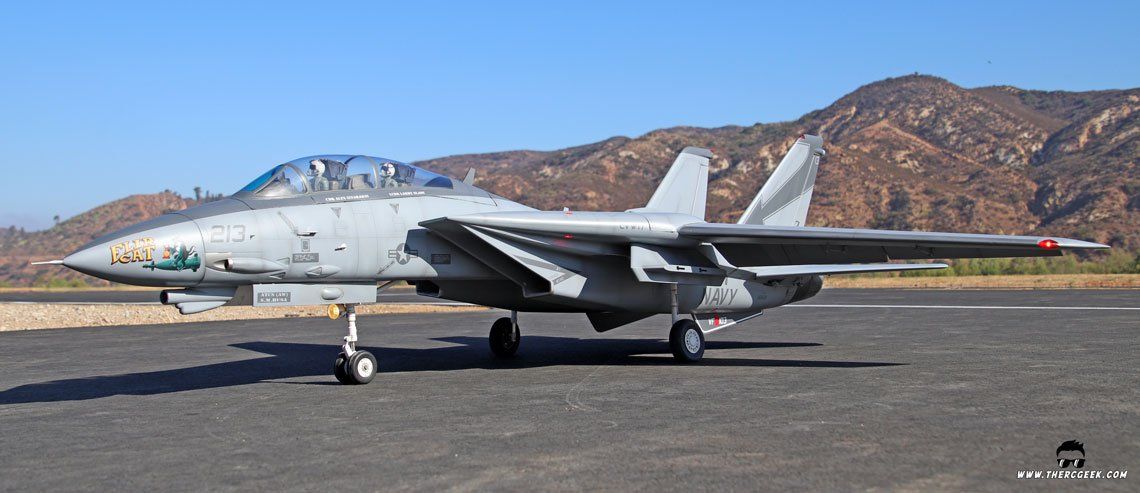