The RC Geek Blog
By: Chris Wolfe
Wait, I can do what?!
3D printing is something that I have been playing with for some time and in one word, it is awesome! Though as a technology, it has been around for a really long time, only within the last few years has it become an accessible tech for most folks. The reason being that the prices of machines have come down dramatically allowing folks access to something that was otherwise cost prohibitive. Also, there are commercial companies now that focus on 3D printing for non-industrial folks like us, plus one can now own a 3D printer for under $1000. So, this is an exciting time as this awesome technology grows in popularity and becomes better and better!
Comparison of the 3D Printed turkey feathers on my JHH Mirage IIIRS to the full size.
As we are going through the Skyray build, 3D printing is something I’m using quite a bit for detailing. I first started seriously experimenting with it on my mirage pushing it to the extent of fully printing the exhaust section turkey feathers. So, with that in mind and having a few 3D printing articles planned in the future, I thought it would be good to start with a good overview of what 3D printing is, the different types of printers and how it can be applied to our models. It’s something you’ll see a bit on my builds. The intent of this article is a general Q&A on 3D printing and how we can utilize the technology on our models to lay the ground work for future articles that I have planned. Also, if you are in need of 3D printing services, I can help! Please send me an email via my contact form with any questions. I can help point you in the right direction and/or help you with some printing/drawings as needed.
What is 3D Printing?
3D printing is the process of applying additive layers of material (typically thermoplastics) under computer control to create a 3-dimensional object. The geometry of the object can be virtually anything and originates typically as a 3D CAD model. There are all types of mediums that can be printed which include metals, ceramics, etc., however, thermoplastics (PLA and ABS primarily) are the most common and least expensive to print. There are also photopolymers (UV cured plastic) that are used to create highly detailed and extremely smooth parts which are useful for model details but are also more expensive to print based on the cost of the material and cost of the 3D printers that use them.
Robo3D FDM Printer
What types of 3D Printers should I know about?
There are a number of different machines out there that use various different processes for printing. However, in the case of our models, the primary types of machines to know about are Fused Deposition Modeling (FDM) extrusion type and Stereolithography (SLA) light polymerized type 3D printers. Printing metals is also being done, but it is still quite expensive, so I’m not sure printing full struts is quite there yet. However, 3D printing is ideal for prototyping gear prior to machining. Also, 3D printing is ideal for making landing gear details and things of that sort. Here’s a quick overview of the two types of printers I deal with for my builds.
Fused Deposition Modeling (FDM)
These are the most commonly known 3D printers. An FDM printer uses a filament (most commonly thermoplastics) that is fed through a hot extruder (to melt the material) that lays down material layer by layer to build the object. The material immediately hardens after extrusion as it is applied and bonds to the previously applied layers. The filament is fed through the extruder typically by a worm drive while the extruder assembly is controlled by stepper motors that move the extruder in the x, y, and z axes. These type of machines can use a number of different materials, but the most common (as far as we’re concerned) are Acrylonitrile Butadiene Styrene (ABS) and Polylactic Acid which are quite inexpensive. The finished part from this type of print is strong and accurate, but typically will have striations in it resulting from each of the printed layers. Depending on the orientation of the part during the print, some aspects of the part can appear “stringy.” This is primarily when trying to print a curved surface that is perpendicular to the extruder (as an example, the top and bottom of a closed sphere). The reason being that the printer is building a curved surface using a series of flat edges (like a topographical map), so the orientation of the part during printing helps minimize this.
FDM Printed Exhausts for a TBM P-40
Stereolithography (SLA)
An SLA printer uses an ultraviolet curable photopolymer resin to build parts one layer at a time. Using an ultraviolet laser, a cross-section of the part is traced onto the surface of the liquid resin for each layer. This in turn cures the resin where the laser tracings were made. This process continues until the entire object has been built. Once completely printed, parts are cleaned in a chemical wash and placed in an ultraviolet oven to fully cure. The finished part from this type of print is very smooth and accurate with extremely fine detail which is ideal for small detail parts for our models, but it can be brittle. Also, these are more expensive prints based on the costs of the photopolymer resins and machines being quite high still so owning one of these at home isn’t the most practical currently. However, there are companies that can help with that (discussed below).
SLA Printed Turkey Feathers for my Mirage
How do I make a 3D printed part?
P-40 Exhaust CAD model
First things first, you need a CAD model of your design before it can be printed. This is done by way of a CAD program where one draws/sculpts their design 3-dimensionally on the computer. There are numerous free programs out there that do the job, or you can purchase one. I have been using Rhino which is a 3D surfacing program and like it quite a bit and find it more intuitive than some other programs out there. It’s not a parametric solid modeling program like SolidWorks or Creo which is both good and not so good depending on who you ask and what their preferred type of modeling is. Ultimately, the best CAD system is the one that works best for you. In the end, whatever you want to print, it must start from a good CAD solid model and be water tight (i.e. no holes in surfaces, misaligned edges, etc.) before being sent to the printer.
Sliced P-40 Exhaust Model
From there, the model is imported into a slicing software that analyzes the model. The software determines how best to print it (defining tool paths, supports, etc.) and generates the g-code that tells the printer how to operate to build the part. If you are sending your part to be printed by a third party, then this is all taken care of by them. Different types of machines require unique settings for the best possible prints. They also require different inputs for operation.
P-40 Exhausts Printing
Once readied in the software, it is sent to the printer and the part is printed. The time required varies based on the complexity, size of the part and the print resolution. This can vary from minutes to multiples of hours. No matter how long, it’s worth the wait!
How can I use 3D Printing for my models?
This is the fun part! Ultimately, anything is possible for our models using 3D printers. It can be simple upgrade/modification parts for servo mounts or things of that sort, or fine detail parts for cockpits, antennas, vents, etc. It can even be taken to the extreme of printing an entire airplane (it has been done). In my case, I prefer to use the technology for detail parts that are otherwise extremely difficult and time consuming to fabricate using traditional modeling materials. A prime example is that just prior to leaving for the 2013 Scale Masters Championships, I had a full set of turkey feathers for my Mirage IIIRS 3D printed (I plan to also do this for the Skyray). The end result far exceeded my expectations and elevated the realism of my airplane considerably. In fact, the craftsmanship judge noted that it was “the best set of turkey feathers he had ever seen on a jet.” Also in preparation of the competition, I made some scale wheel hubs as well that included the lug nuts that exist radially around the hub and valve stem in full detail. All of these details added considerable realism to the airplane which helped make it a much more convincing scale model and I believed helped notably on my static judging score.
Do I need to own my own 3D Printer?
As fun as they are, it’s not necessary to own your own 3D printer. Depending on the type of print, it may not be practical to own the type of 3D printer that is necessary (i.e. SLA). That being said, there are guys like me that will help print models for you (I can turn around prints in a day or two, email me for more info ) and companies out there like Shapeways.com (2 week turnaround typically) as well that allow us to print anything we need to. That being said, I do own a 3D printer and absolutely love it! It is a ROBO 3D which is an FDM machine that prints PLA and ABS and I am happy to help others with their modeling and printing needs. It works great for prototyping as well as for some detail parts too. However, to print extremely small and fine detail parts for our models it requires an expensive SLA type machine that uses a very expensive photopolymer material. So, that is where companies like Shapeways come in as they have these machines and offer printing services for these type of prints. I have printed a number of items from Shapeways and can attest to the quality and extreme detail they produce, but this is also the more expensive print to make. So, for items that don’t make sense to print on my own machine or where I need the smooth finish, I go to Shapeways for the ultra detail when needed. A good example of this are the turkey feathers on my mirage shown below in it’s various stages.
Robo3D Extrusion Assembly
If you can model it, you can print it!
In closing, as we move along with the Skyray build, we’ll come back to 3D printing quite a bit. It’s a great process and has really changed what can be done with our scale models. Also, if you do have a 3D printing need or are curious about some CAD modeling or just have some general questions, please feel free to shoot me an email as I am happy to help! I have access to a couple of printers (including my own) and can turn parts around very quickly (within a day or two).
The post Adventures in 3D Printing – Ep1 appeared first on The RC Geek.
The RC Geek Blog is your place to learn about all aspects of the RC hobby. Learn to build, design, drive or fly that RC project you’ve always wanted to build, but have been intimidated to try. This blog is here to help you on your journey and provide tips and tricks as you go! My hope is to inspire builders both experienced and new! So, welcome, please look around, it’s an exciting beginning! I’m currently documenting my latest competition scale RC jet build, a Mark Frankel F4D Skyray, along with some other fun tips and videos. If you can’t find what you’re looking for on this front page, click on any of the categories to the right and it will show just posts related to those categories. Please feel free to add comments and/or contact me directly if you have questions, I’m here to help! And don’t forget to check out my YouTube Channel, I post new videos every week!
Subscribe To Our Blog Now
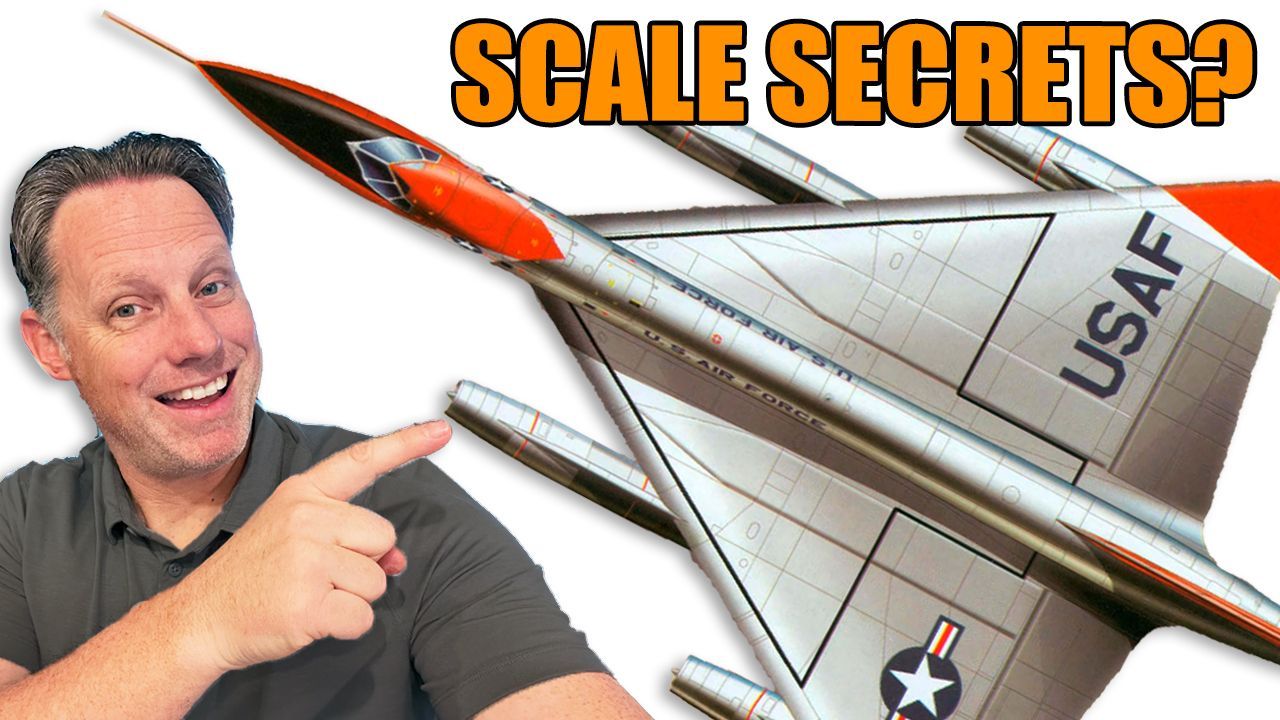
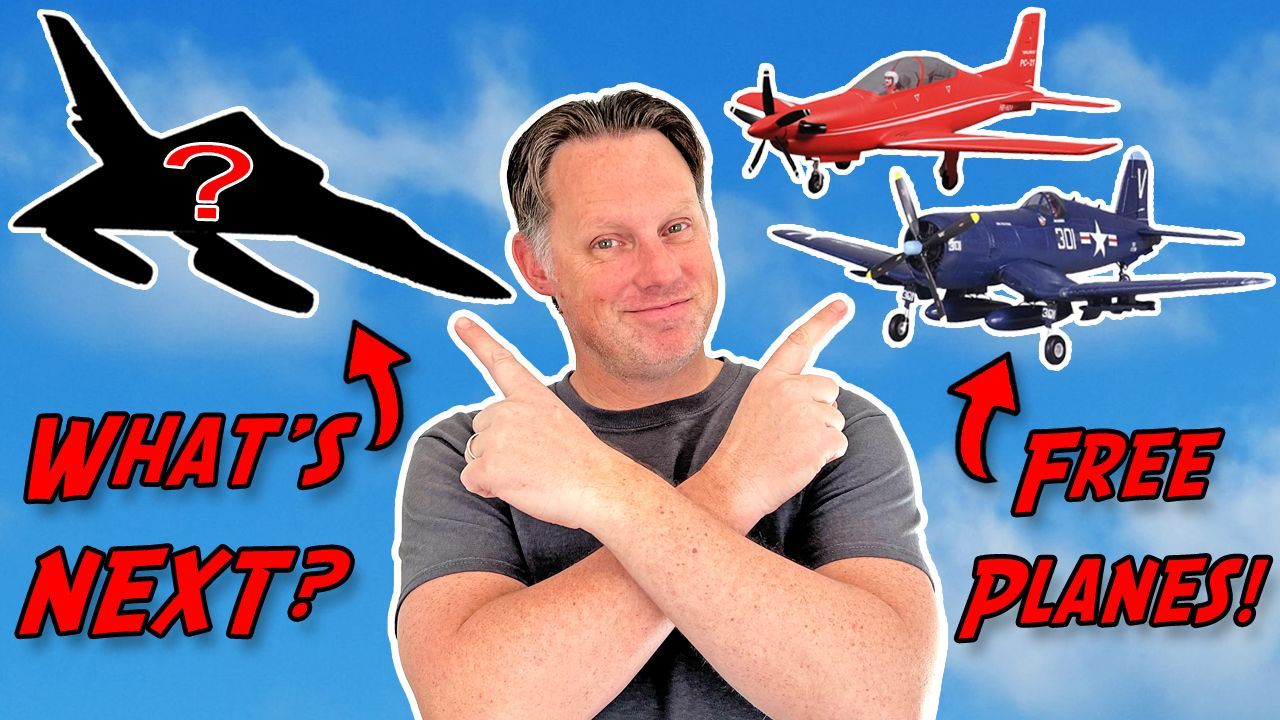
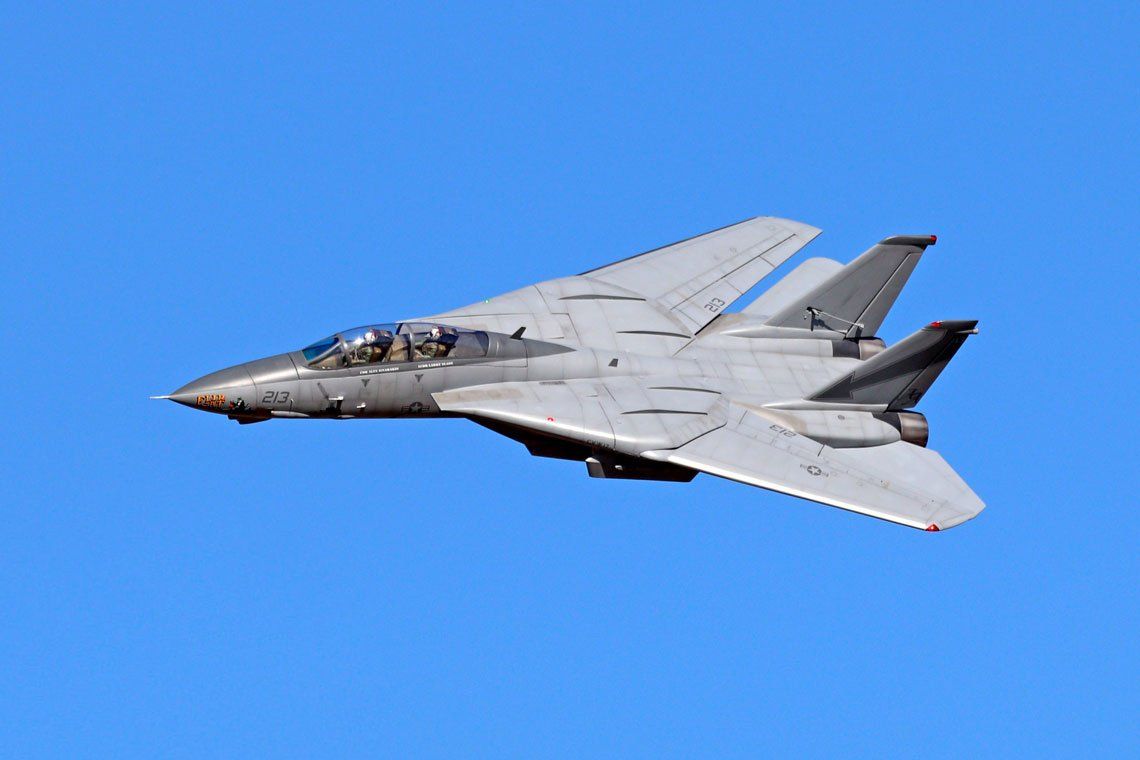
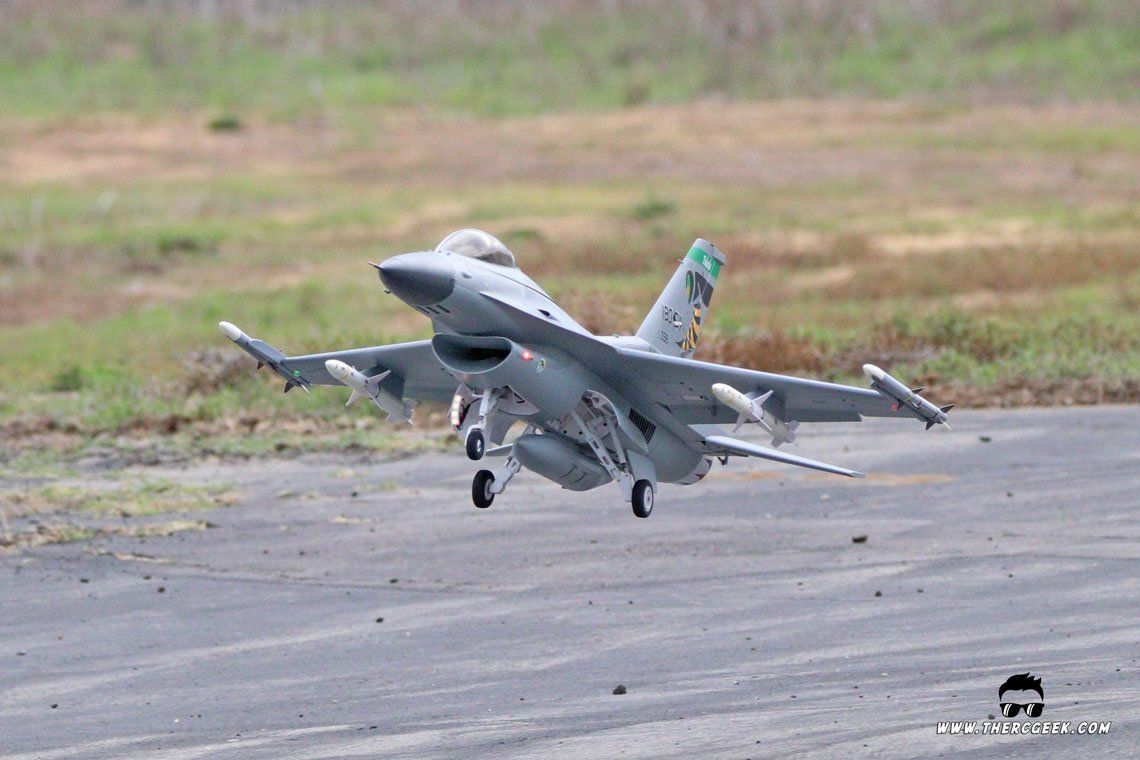
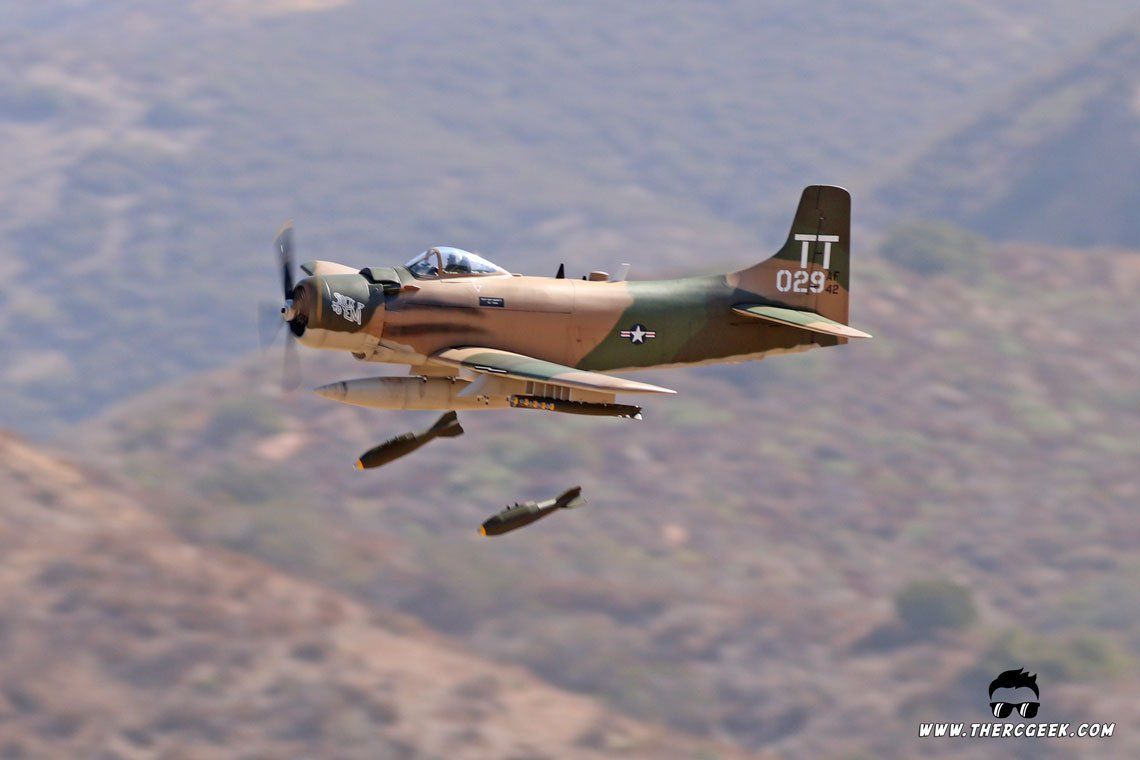
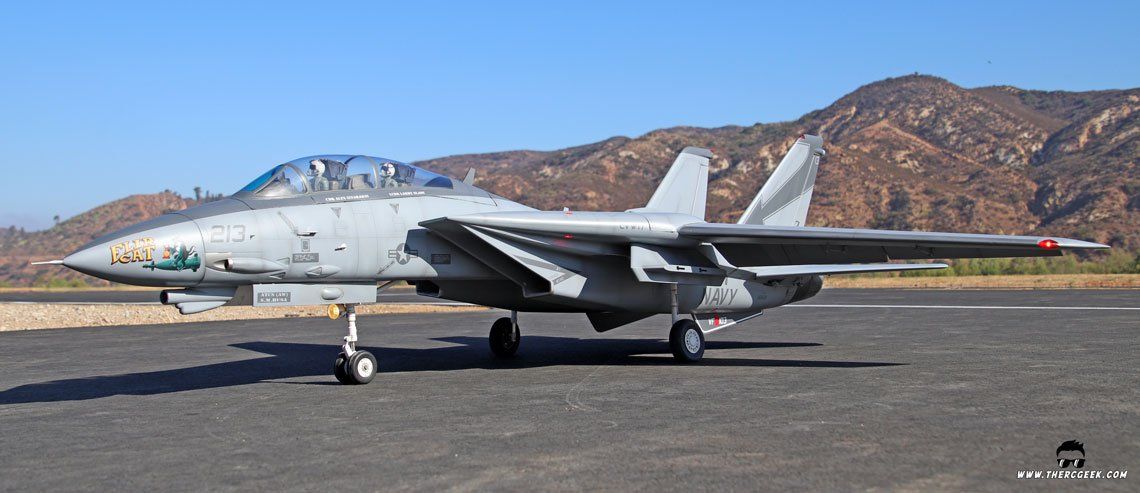