The RC Geek Blog
By: Chris Wolfe
The beauty is in the details…
As promised in my How to Repair Fiberglass and Fibgerglassed Parts article , here’s a little tutorial on some of the detail parts I had to re-scratch build while repairing my Mirage IIIRS earlier this year. These include some of the very distinctive pitot tubes and antennas that are exhibited on the nose section of the full-sized aircraft. In all the searching we did of the crash site when the airplane went in, the original parts were just nowhere to be found…a sacrifice to the three angry bushes that swallowed my airplane I suppose! Also, if you missed it, be sure to check out my coverage from the US Scale Masters Championships as I competed with my fully repaired Mirage and somehow in the process came out of the competition finishing 1st in Expert being named the Grand National Champion! What an amazing weekend! It was such a great event with a wonderful and very talented group of scale modelers, I can’t wait to go back!
CHOOSING THE RIGHT MATERIALS
When we talk about detail parts, we need to talk about materials selection. Obviously, any materials can be used, but when dealing with parts that are protruding from an airplane, we need parts with stiffness and resilience to repeated abuse. Let’s face it, these parts are going to get knocked and bumped repeatedly! For pitot tubes, my go-to is to use concentric brass tubes and brass planks. I use silver solder to solder everything together and I guarantee, you’ll break the airplane before you break the pitot tubes. For antennas, I turn to basswood since it’s easy enough to sand, but hard enough to withstand most bumps.
What about 3D printing you ask? For antennas, 3D printing is definitely a good way to go especially if printing from PLA since it’s extremely hard. I didn’t go that route in this case simply because it was quicker for me to simply carve out the one antenna I needed from basswood. The quicker I could repair this bird, the quicker I could get back to doing more fun stuff! For pitot tubes, it could go either way regarding 3D printing. For small and very fine detail parts, SLA would be the printer medium of choice since it is capable of very fine and incredibly high resolution prints. Unfortunately, it can be brittle, especially for really small parts (the pitot tubes are 1/16″ diameter on my airplane) so one knock and that nicely printed and painted pitot tube is most likely going to break. For larger models with larger diameter pitot tubes, it’s a little more viable option but it’s really hard to beat brass for its resilience and these pitot tubes are easy to make and can potentially be made quicker than it takes to model one for printing.
HOW TO MAKE ANTENNAS
Antennas are a simple detail that can really add a lot to a model…and they’re easy to make. It’s simply a matter of cutting out the appropriate antenna side profile from some 1/8″ thick basswood (or whatever is necessary to create the specific antenna) and then sanding an appropriate cross section profile into it. Antennas on jet aircraft rarely have a traditional airfoil cross section but rather have a more diamond type shape. It’s best to do a little research to see what it looks like, but even just a straight plank without any contours works well and is quite convincing. I’ll typically start with a drawing of the part and use that to cut out the basic shapes of the antenna. In the case here, I needed an antenna as well as a base fairing.
For preparing the basswood for paint, you can simply apply a couple coats of primer , lightly sand it and then apply a couple more coats repeating this process until the wood grain is filled in. Gluing the antenna onto the airframe is done by cutting a slot into the fuselage and the antenna glued into it with epoxy. There should be about 1/8″ material that extends into the fuselage so there won’t be any issues with it sheering off…antenna dysfunction is a serious problem, don’t let it happen to you! Once installed, and happy with the installation, the antenna was painted. On this particular airplane, it was black so nothing special was needed in terms of finish.
HOW TO MAKE PITOT TUBES
As noted above, I prefer to use brass tubes for making pitot tubes. I use concentric tubing cut to strategic lengths to make whatever radial shapes are necessary to match the scale profiles. In the case of the mirage, the pitot tube needing to be made was on the lower side. To look at it, it has two distinct diameters with the larger diameter reducing down to the smaller and is mounted to a rearward swept pylon. For the larger diameter, I used a 1/8″ diameter tube and the smaller diameter a 1/16″ diameter tube. To get the radial taper a 3/32″ diameter tube was glued with thin CA inside the larger 1/8″ diameter tube and the taper was sanded on each end using my bench sander while spinning the parts in a drill. Also, that intermediate 3/32″ tube serves to hold the smaller 1/16″ diameter tube pitot which protrudes forward. With the radial tapers sanded in place, the 1/16″ diameter tube was glued into the sanded set of tubes. From there, I soldered a 1/2″ wide by 1/16″ thick brass plank (using silver solder ) onto the pitot tube assembly.
From there, the pitot tube was prepped for painting with a little primer and then epoxied into the airplane. Just like the antennas, it’s best to grind a slot into the fuselage to receive the pitot base and then epoxy it in place with a small fillet on each side internally. All of the pitot tubes on the airplane were made how we’ve discussed. To get the metallic finish on the front, I used some ALCLAD II “Dark Aluminum” paint. If you’ve never used it, it’s awesome paint that will get you a nice and convincing metallic finish in most cases. And, it’s really durable too.
REPAIRED AT LAST…
These details were the final pieces needed in getting the mirage back in working order again. As noted in my last article, I swapped out the E-Turbax for a JetFan120 and Neu 1917/1y motor which has been an excellent combination in the airplane especially for competition. With the lower current draw from the fan (with similar performance to what I had with the E-Turbax), I was able to extend my flight times during competition without too much worry which made getting all of the maneuvers in stress free while having to make additional circles for traffic avoidance. It was a great improvement to have, especially at the USSM Championships!
From here, with the USSM championships
done and all the repairs (and hopefully bugs) worked out, it’s time to get some building in on something new finally! I hope next time to have our next installment on our Freewing Mirage 2000 to Kfir kit bash. It is currently on the bench and underway! Until then, this is your 2016 US Scale Masters National Champion signing off.
I’ll see you guys at the field!
The post Tutorial – How to Make Detail Antennas and Pitot Tubes appeared first on The RC Geek.
The RC Geek Blog is your place to learn about all aspects of the RC hobby. Learn to build, design, drive or fly that RC project you’ve always wanted to build, but have been intimidated to try. This blog is here to help you on your journey and provide tips and tricks as you go! My hope is to inspire builders both experienced and new! So, welcome, please look around, it’s an exciting beginning! I’m currently documenting my latest competition scale RC jet build, a Mark Frankel F4D Skyray, along with some other fun tips and videos. If you can’t find what you’re looking for on this front page, click on any of the categories to the right and it will show just posts related to those categories. Please feel free to add comments and/or contact me directly if you have questions, I’m here to help! And don’t forget to check out my YouTube Channel, I post new videos every week!
Subscribe To Our Blog Now
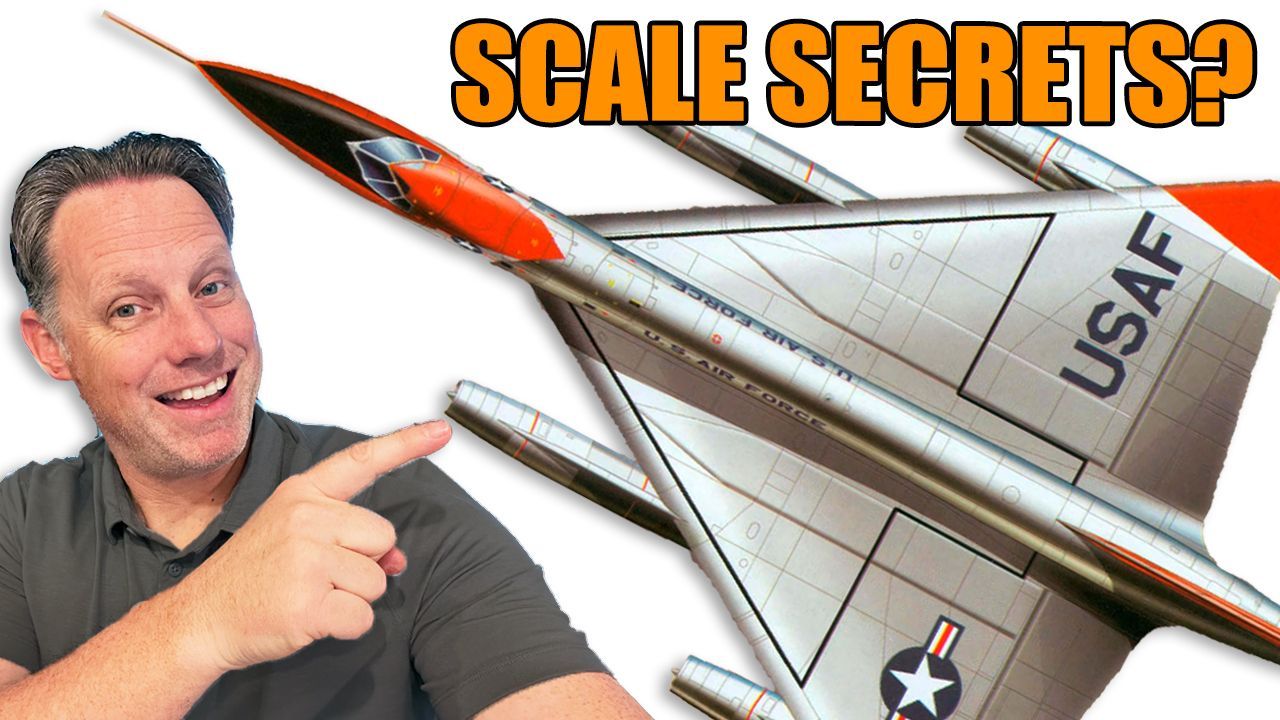
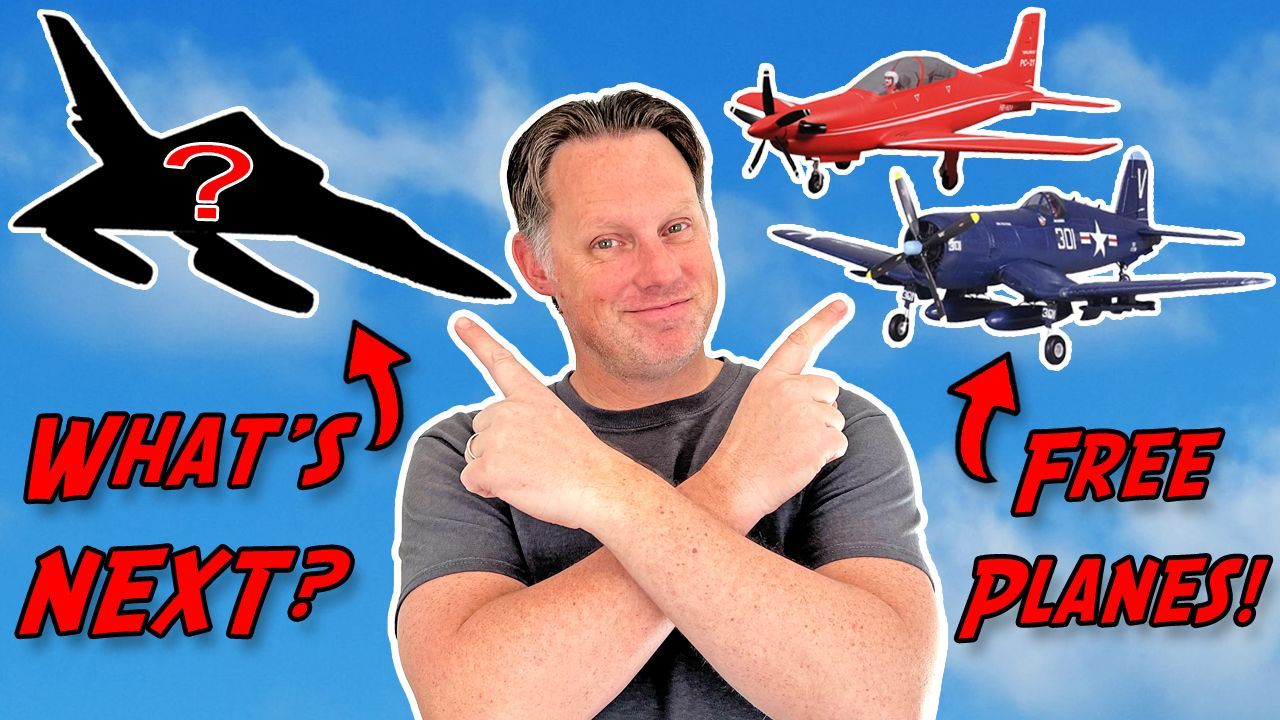
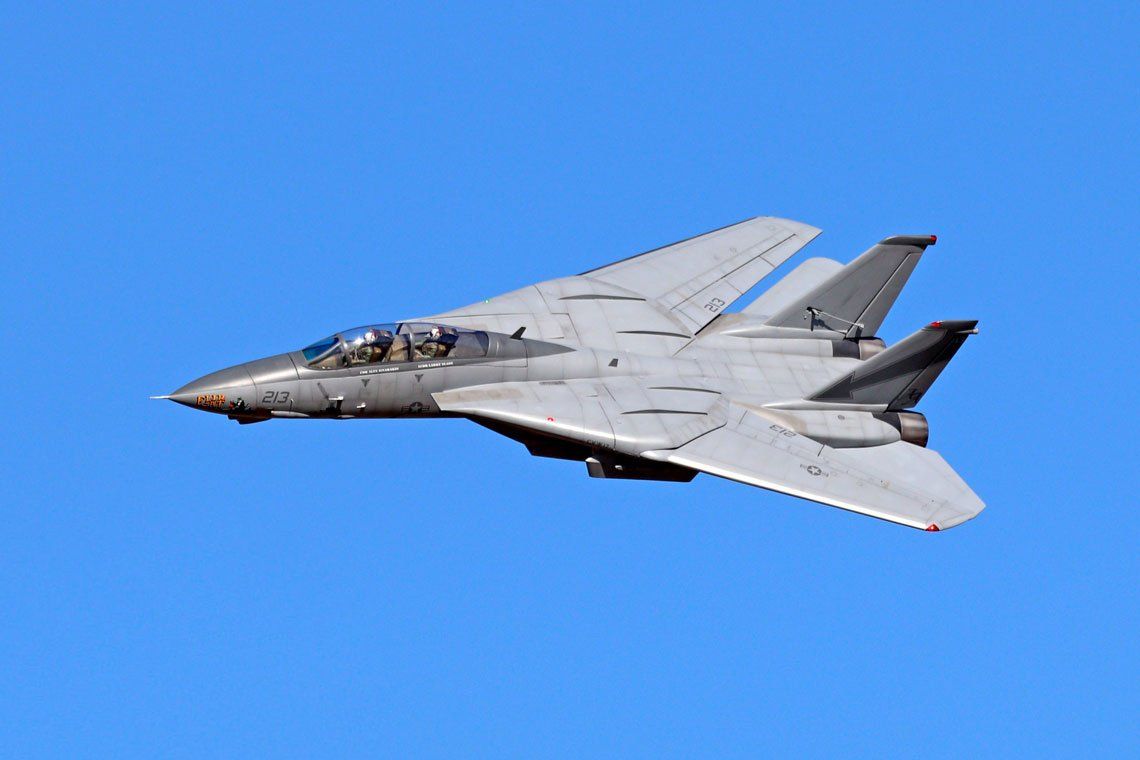
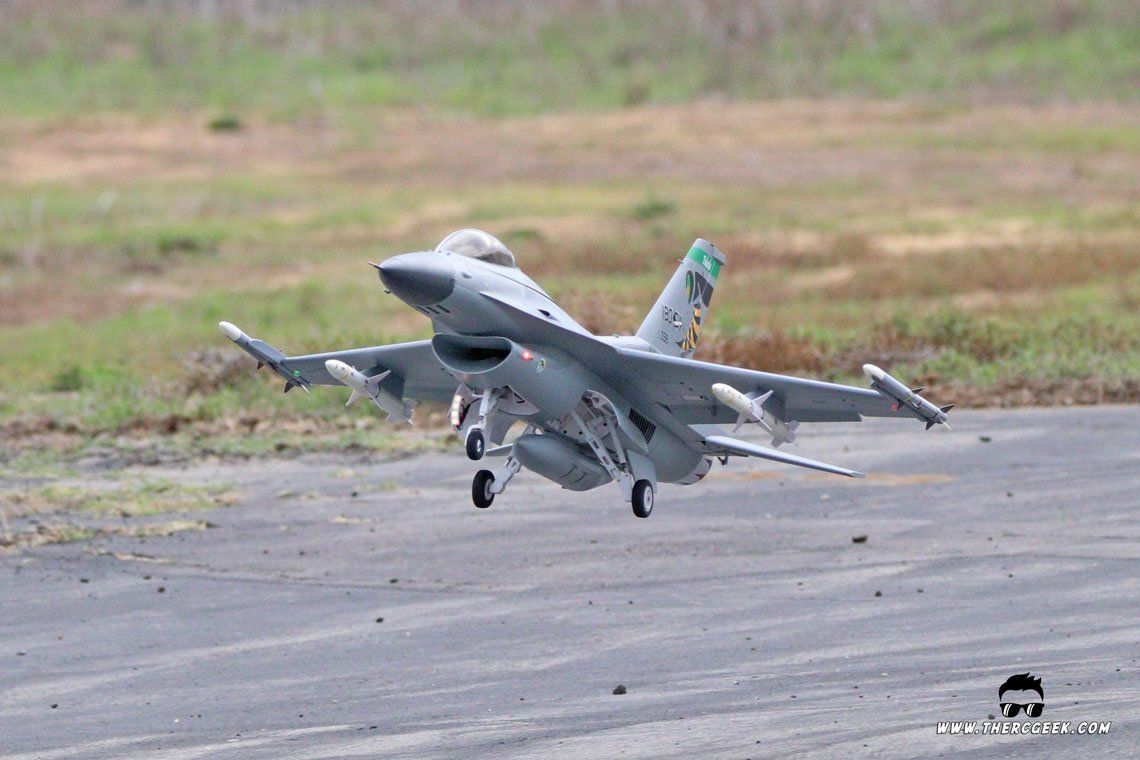
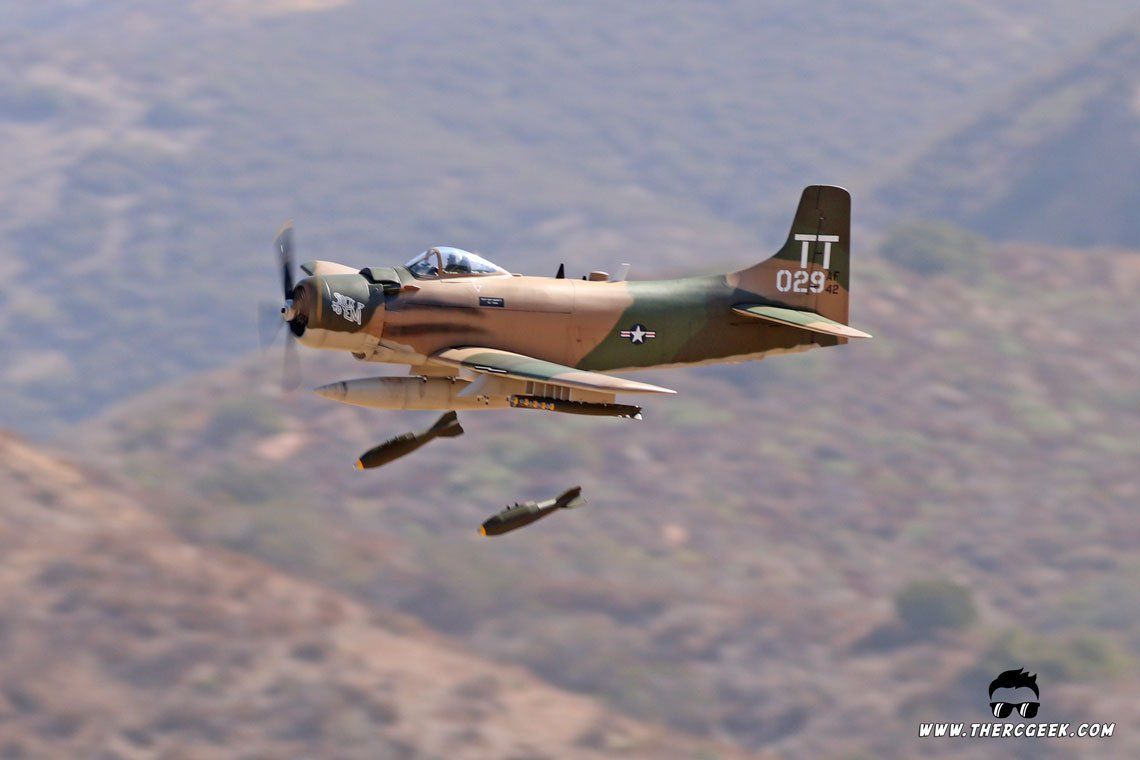
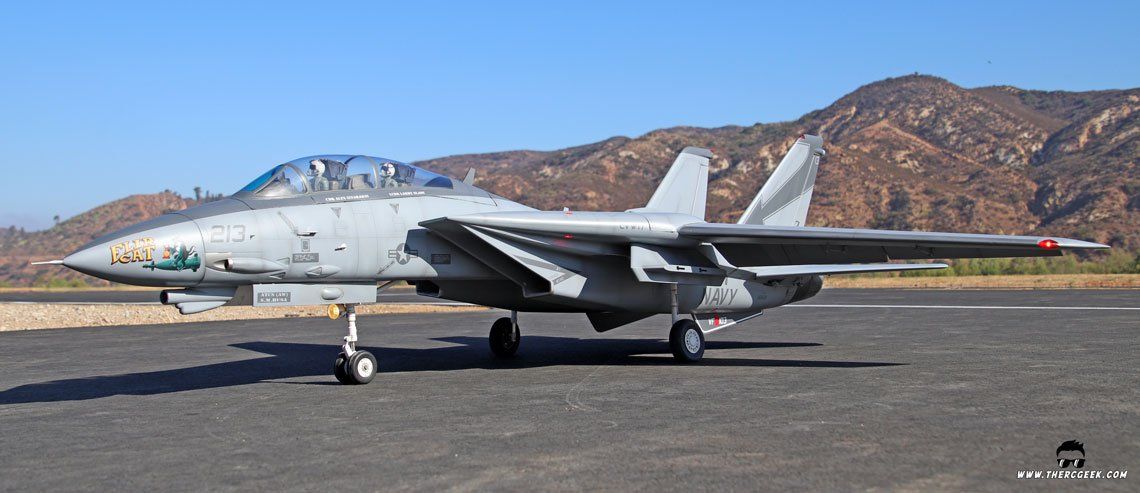